PRODUCT PARAMETERS
Description
Brief introduction of High quality grinding ball mill part durable ball mill pinion shaft
Ball mill is a kind of equipment used to crush or grind materials to very fine powder, which is widely used in mining, cement, chemical industry, etc. High quality grinding ball mill part durable ball mill pinion shaft refers to all kinds of parts and components which are necessary to ensure the normal operation of the ball mill, including liner plate, grinding balls, gears, bearings and so on.
Features and advantages of High quality grinding ball mill part durable ball mill pinion shaft
Strong durability: Made of high-quality materials and under strict quality control, it ensures high wear resistance and long service life of spare parts.
Good interchangeability: The standardized design makes the spare parts interchangeable between different types of ball mills, simplifying the maintenance process.
Optimized design: Customised design according to the actual working conditions, which improves the working efficiency and reduces energy consumption at the same time.
Easy to install and maintain: reasonable structure, convenient for users to quickly replace and repair, reduce downtime.
Stable performance: Precision machining and rigorous testing ensure stable performance even in harsh environments.
(High quality grinding ball mill part durable ball mill pinion shaft)
Specification of High quality grinding ball mill part durable ball mill pinion shaft
The high-quality grinding ball mill pinion shaft is a critical component designed for reliable power transmission in ball mill systems, ensuring optimal performance in abrasive and high-load environments. Crafted from premium-grade alloy steel, such as 42CrMo or equivalent, this pinion shaft offers exceptional strength, wear resistance, and fatigue durability. The material undergoes advanced heat treatment processes, including carburizing, quenching, and tempering, achieving a surface hardness of 58-62 HRC for superior wear resistance while maintaining a tough core hardness of 28-32 HRC to withstand impact and bending stresses. Precision-machined gear teeth with an involute profile ensure smooth engagement with the ring gear, minimizing vibration and noise. The gear teeth adhere to AGMA or ISO accuracy standards (Grade 6 or higher), with a module range of 10-32, pressure angles of 20°, and customizable tooth counts to match specific mill configurations. Dimensional specifications include shaft diameters from 100 mm to 500 mm and lengths up to 3000 mm, tailored to fit various mill sizes. The shaft’s torque capacity ranges from 10,000 Nm to 150,000 Nm, supporting high rotational speeds (up to 1,500 RPM) without deformation. Surface treatments like phosphating or nitriding enhance corrosion resistance and reduce friction. Rigorous quality control involves ultrasonic testing, magnetic particle inspection, and dimensional checks to eliminate defects. Compatible with mining, cement, and chemical industries, this pinion shaft is engineered for seamless integration with leading ball mill brands, offering extended service life under continuous operation. Customization options include flanged designs, keyway configurations, and bespoke material grades. Backed by ISO 9001 certification, this durable pinion shaft ensures reduced downtime and maintenance costs, making it ideal for heavy-duty grinding applications.
(High quality grinding ball mill part durable ball mill pinion shaft)
Applications of High quality grinding ball mill part durable ball mill pinion shaft
High-quality grinding ball mill parts, such as durable ball mill pinion shafts, are critical components in industrial grinding operations, ensuring efficiency, longevity, and reliability. The pinion shaft plays a pivotal role in transmitting rotational power from the motor to the ball mill’s girth gear, enabling the mill to crush and grind raw materials into fine powders. Designed for heavy-duty applications, these precision-engineered shafts are ideal for industries like mining, cement production, chemical processing, and mineral beneficiation, where continuous operation under extreme conditions is the norm.
In mining and mineral processing, ball mill pinion shafts are subjected to abrasive environments and high torque loads. A durable pinion shaft, crafted from high-grade alloy steel and heat-treated for enhanced hardness, resists wear, deformation, and fatigue, minimizing downtime. Its precise machining ensures optimal alignment with the girth gear, reducing vibration and noise while improving energy efficiency. This reliability is vital for processing ores like gold, copper, and iron, where uninterrupted operation directly impacts productivity.
Cement manufacturing relies on ball mills to grind clinker and additives into cement. Here, pinion shafts endure high temperatures and heavy mechanical stress. A robust pinion shaft with anti-corrosion coatings and superior load-bearing capacity maintains performance in harsh thermal cycles, extending service life and reducing maintenance costs. Similarly, in the chemical industry, where ball mills process corrosive or reactive materials, corrosion-resistant pinion shafts prevent premature failure, ensuring consistent particle size distribution for quality control.
Power generation plants use ball mills to pulverize coal for combustion. A high-quality pinion shaft withstands continuous high-speed rotation and shock loads, ensuring stable coal grinding for efficient energy production. Its durability also lowers replacement frequency, offering long-term cost savings.
Key features of premium ball mill pinion shafts include precision gear teeth profiles for smooth meshing, advanced surface treatments for wear resistance, and rigorous quality testing to meet industry standards. By investing in durable pinion shafts, industries enhance operational efficiency, reduce unplanned downtime, and achieve higher ROI in grinding processes. Whether for raw material processing or fine powder production, a reliable pinion shaft is indispensable for sustaining peak mill performance.
Company Introduction
Established in 2007, Excavator Attachments Heavy Machinery Co.,ltd. focus on metal research and mining machinery spare parts. 2 factories over an area of 13,300 square meters, based on 100+ sets of equipment, our production capacity reaches 12000 Tons/Year. has passed ISO 9001 quality managment system certification in 2008.
Our mainly products are dragline excavator spare parts,rotary kiln spare parts, large modulus gear (gear shaft), gearbox ect. 40+ patents with over 45 years experience to help focus on improve the service life of spare parts. We belive that more than 80% reason of mechanical parts’ working life depends on hot processing (steel making/forging/casting/welding/heat treatment). Eight material engineers will control the quality from the original resource.
If you are interested, please feel free to contact us.
Payment
L/C, T/T, Western Union, Paypal, Credit Card etc.
Shipment
By sea, by air, by express, as customers request.
5 FAQs of High quality grinding ball mill part durable ball mill pinion shaft
What makes the ball mill pinion shaft durable? The durability stems from high-grade alloy steel or forged high-carbon steel, combined with heat treatments like carburizing or induction hardening. These processes enhance surface hardness while maintaining a tough core to handle heavy loads. Precision machining ensures smooth gear engagement, reducing friction and wear, while corrosion-resistant coatings or treatments protect against harsh operating environments.
What materials are used in manufacturing the pinion shaft? It is typically forged from high-carbon steel or alloy steel, chosen for strength and fatigue resistance. Advanced surface treatments like carburizing create a hardened outer layer for wear resistance, while the core remains ductile to absorb impacts. Some variants use induction hardening for targeted surface durability, ensuring longevity even under continuous stress.
How do I maintain the pinion shaft for optimal lifespan? Regular lubrication with high-viscosity grease minimizes friction and heat. Periodically check gear alignment and meshing to prevent uneven wear. Monitor for vibrations, unusual noises, or overheating, which signal misalignment or lubrication issues. Avoid overloading the mill, as excessive stress accelerates wear. Inspect the shaft and gears during routine maintenance to address minor issues before they escalate.
Is the pinion shaft compatible with any ball mill model? Compatibility depends on specifications like shaft dimensions, number of gear teeth, gear module, and bore diameter. Always cross-reference these parameters with your ball mill’s requirements. Customizable options are available for non-standard setups, including tailored dimensions or material upgrades to suit specific operational demands.
What are signs of pinion shaft wear or failure? Common indicators include grinding noises, excessive vibration, overheating, or visible damage like pitting, cracks, or chipped teeth on the gear. Reduced milling efficiency or irregular mill rotation may also point to shaft issues. Immediate replacement is crucial to prevent collateral damage to the gear ring or motor, ensuring uninterrupted operation and avoiding costly downtime.
(High quality grinding ball mill part durable ball mill pinion shaft)
REQUEST A QUOTE
RELATED PRODUCTS
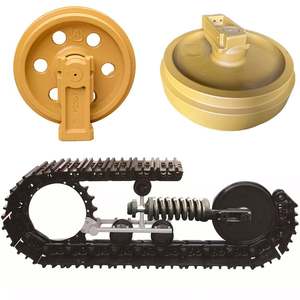
Iron Ore Ball Mills Gypsum Grinding Ball Mill Machine Gold Provided AC Motor Spare Part of Cement Factory Steel Ball Mill 1year
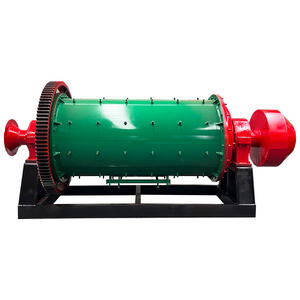
Gear Shaft For Ball Mill Spline Gear Shaft Mining Spare Parts Gear Shaft For Gearbox
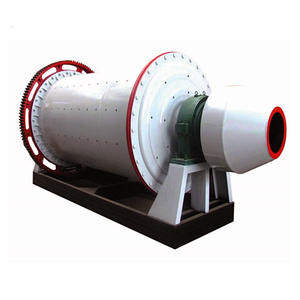
High Chrome manganese Alloy cement quartz copper and gold ore ball mill liner wear plate spare parts
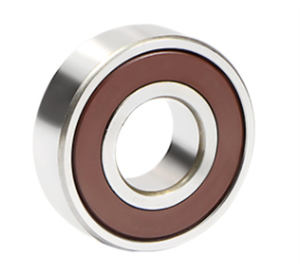
Overflow ball mill Mining Equipment Machine s/Grinding Mill/Rod Mill For Hematite, Iron Ore, Bentonite, Limestone, Cement
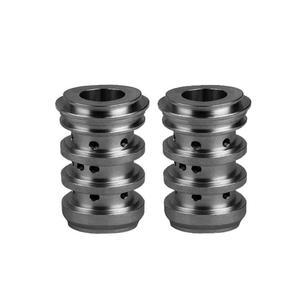
Mining Equipment Spares Hollow Shaft Discharge Shaft for Ball Mill
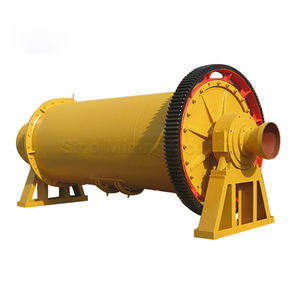