PRODUCT PARAMETERS
Description
Brief introduction of Factory Direct Supply High Quality ball mill with rubber liner ball mill
Ball mill is a kind of equipment used to crush or grind materials to very fine powder, which is widely used in mining, cement, chemical industry, etc. Factory Direct Supply High Quality ball mill with rubber liner ball mill refers to all kinds of parts and components which are necessary to ensure the normal operation of the ball mill, including liner plate, grinding balls, gears, bearings and so on.
Features and advantages of Factory Direct Supply High Quality ball mill with rubber liner ball mill
Strong durability: Made of high-quality materials and under strict quality control, it ensures high wear resistance and long service life of spare parts.
Good interchangeability: The standardized design makes the spare parts interchangeable between different types of ball mills, simplifying the maintenance process.
Optimized design: Customised design according to the actual working conditions, which improves the working efficiency and reduces energy consumption at the same time.
Easy to install and maintain: reasonable structure, convenient for users to quickly replace and repair, reduce downtime.
Stable performance: Precision machining and rigorous testing ensure stable performance even in harsh environments.
(Factory Direct Supply High Quality ball mill with rubber liner ball mill)
Specification of Factory Direct Supply High Quality ball mill with rubber liner ball mill
The Manufacturing Facility Straight Supply Top Quality Round Mill with Rubber Liner is developed for efficient grinding and longevity throughout commercial applications. Engineered for mining, cement, ceramics, and chemical processing, this round mill incorporates innovative innovation with robust building and construction to supply consistent efficiency. The rubber lining improves wear resistance, decreases sound, and minimizes energy usage, making it suitable for both dry and damp grinding procedures.
** Specs: **.
– ** Capacity: ** Available in versions ranging from 0.5 T/H to 100 T/H, personalized to satisfy certain production demands.
– ** Motor Power: ** Geared up with high-efficiency electrical motors (22 kW to 4500 kW), guaranteeing smooth procedure and low energy intake.
– ** Drum Dimensions: ** Requirement drum diameters from 900 mm to 4500 mm, with sizes differing based upon ability needs.
– ** Rotation Speed: ** Adjustable in between 15-28 RPM, maximized for product type and grinding effectiveness.
– ** Product Compatibility: ** Processes ores, concrete clinker, silicate items, plant foods, ferrous/non-ferrous steels, and glass porcelains.
– ** Rubber Lining Density: ** 30 mm to 50 mm, crafted from state-of-the-art wear-resistant rubber for extended life span.
– ** Framework: ** Durable steel structure with anti-vibration mounts, making sure stability and lowering functional noise.
– ** Discharge System: ** Overflow or grate discharge choices for specific particle dimension control.
** Secret Features: **.
The rubber lining system eliminates metal-to-metal call, lowering maintenance expenses and protecting against contamination. Its shock-absorbing properties improve equipment longevity, while the anti-corrosion style suits rough environments. The mill operates with minimal warmth generation, preserving material stability.
** Applications: **.
Suitable for grinding abrasive and high-impact products in mining, concrete manufacturing, and chemical markets. Suitable for additional grinding after crushing procedures.
** Advantages: **.
– ** Low Upkeep: ** Rubber linings last longer than standard steel liners, lowering downtime.
– ** Energy Effectiveness: ** Optimized electric motor and design reduced power consumption by approximately 20%.
– ** Sound Reduction: ** Rubber moistens operational sound, improving office safety.
– ** Personalization: ** Adjustable rate, liner thickness, and discharge mechanisms to match application demands.
** Quality control: **.
Manufactured under stringent quality control requirements, making use of premium-grade materials. Each mill undertakes extensive screening for efficiency and sturdiness.
** Guarantee & Support: **.
Backed by a 2-year warranty, with life time technological assistance and accessibility to extra components. Factory-direct pricing makes certain cost-effectiveness without endangering quality. This ball mill is a trusted, lasting remedy for markets seeking high efficiency and decreased functional prices.
(Factory Direct Supply High Quality ball mill with rubber liner ball mill)
Applications of Factory Direct Supply High Quality ball mill with rubber liner ball mill
A factory direct supply high-grade ball mill with a rubber liner is a flexible and long lasting grinding solution created for industries calling for reliable product processing. The rubber-lined round mill integrates the toughness of a conventional round mill with advanced rubber lining technology, enhancing performance, long life, and functional efficiency. Below are vital applications of this equipment throughout sectors:
** Mining and Mineral Handling **: Rubber-lined round mills are widely utilized to grind ores, such as gold, copper, and iron, right into great powders for additional handling. The rubber liner minimizes wear brought on by unpleasant products, expanding the mill’s life-span. Its corrosion-resistant buildings also make it perfect for damp grinding processes involving chemicals or dampness.
** Cement and Building **: In cement production, the round mill grinds basic materials like limestone and clinker. The rubber lining reduces energy consumption by enhancing grinding efficiency and moistening sound levels, producing a much safer workplace. Its shock-absorbing residential or commercial properties secure the mill structure from resonances during high-capacity operations.
** Chemical Industry **: For refining chemicals, pigments, or fertilizers, the rubber liner avoids contamination brought on by metal-to-material call. Its non-reactive nature guarantees pureness in delicate chemical reactions, while its longevity takes care of corrosive materials effectively.
** Ceramics and Glass Manufacturing **: The exact grinding of silica, feldspar, and ceramics demands consistency. Rubber liners offer smooth grinding surface areas, decreasing bit dimension variability and boosting product top quality.
** Recycling and Waste Management **: Rubber-lined ball mills process recyclable products like electronic waste, slag, or construction debris. The liner’s versatility fits off-and-on designed materials, while its wear resistance handles difficult reusing applications.
** Benefits of Rubber Liners **: Contrasted to steel liners, rubber liners provide 30-50% longer service life, decreased upkeep prices, and up to 20% lower energy intake. They also operate silently, decreasing sound pollution.
Factory-direct supply makes sure cost-effectiveness, quality assurance, and personalization choices. These mills are tailored to client needs, with flexible rotation rates, liner density, and chamber dimensions. Suitable for both small and industrial procedures, the rubber-lined sphere mill is a reliable, environment-friendly service for grinding challenges throughout sectors. Its adaptability and performance make it a foundation of contemporary material processing.
Company Introduction
Established in 2007, Excavator Attachments Heavy Machinery Co.,ltd. focus on metal research and mining machinery spare parts. 2 factories over an area of 13,300 square meters, based on 100+ sets of equipment, our production capacity reaches 12000 Tons/Year. has passed ISO 9001 quality managment system certification in 2008.
Our mainly products are dragline excavator spare parts,rotary kiln spare parts, large modulus gear (gear shaft), gearbox ect. 40+ patents with over 45 years experience to help focus on improve the service life of spare parts. We belive that more than 80% reason of mechanical parts’ working life depends on hot processing (steel making/forging/casting/welding/heat treatment). Eight material engineers will control the quality from the original resource.
If you are interested, please feel free to contact us.
Payment
L/C, T/T, Western Union, Paypal, Credit Card etc.
Shipment
By sea, by air, by express, as customers request.
5 FAQs of Factory Direct Supply High Quality ball mill with rubber liner ball mill
What is a rubber liner ball mill? A rubber liner ball mill is a grinding machine equipped with rubber liners instead of traditional metal liners. It is designed for reducing material size by rotating a cylinder filled with grinding media, such as steel balls. The rubber lining absorbs impact, minimizes noise, and reduces wear on the mill’s interior. This makes it ideal for processing abrasive or corrosive materials while extending the equipment’s lifespan.
What are the advantages of rubber liners over steel liners? Rubber liners offer superior corrosion resistance, reduced operational noise, and lower energy consumption compared to steel liners. They are less prone to cracking under heavy impact, ensuring fewer maintenance interruptions. Rubber’s flexibility also minimizes grinding media and mill shell wear, lowering long-term costs. Additionally, rubber liners are lighter, simplifying installation and reducing strain on the mill structure.
Which industries benefit most from rubber liner ball mills? Rubber liner ball mills are widely used in mining, ceramics, cement, chemicals, and pyrotechnics. They excel in processing abrasive ores, silica sand, limestone, and corrosive substances like acids or salts. Industries prioritizing energy efficiency, noise reduction, and equipment durability often opt for rubber-lined mills to enhance productivity and reduce downtime.
How durable are rubber liners, and how are they maintained? Rubber liners typically last 2–3 times longer than steel liners in abrasive environments. Maintenance involves regular inspections for wear, tear, or chemical degradation. Damaged sections can be replaced individually without dismantling the entire mill, reducing downtime. Cleaning with water or mild solvents prevents material buildup. Proper alignment and avoiding overloading the mill further extend liner life.
Can the rubber liner ball mill be customized? Yes. Factory direct supply allows customization of rubber liner thickness, hardness, and pattern to match specific grinding needs. Mills can be tailored in size, rotation speed, and capacity. Clients can also choose rubber compounds resistant to specific chemicals or temperatures. Custom designs ensure optimal performance for unique operational requirements while maintaining cost-efficiency through direct manufacturer collaboration.
(Factory Direct Supply High Quality ball mill with rubber liner ball mill)
REQUEST A QUOTE
RELATED PRODUCTS
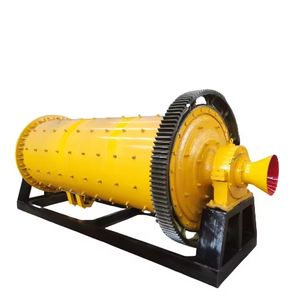
Customized Mining Machine Parts Main Auxiliary Rotary Kiln Ball Mill Pinion Device Large Spur Big Helical Gear Shaft Assembly
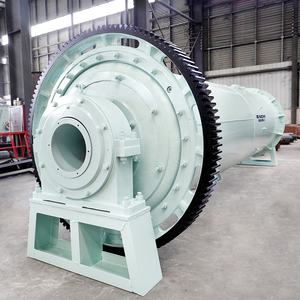
Cast White Iron AS 2027 CrMo 15 Grinding Ball Mill liner Wear Plate
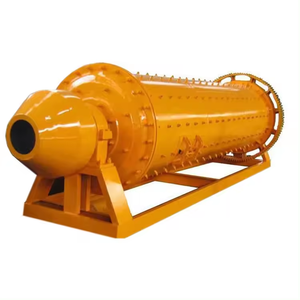
Small Ball Mill Grinding Machine with New Motor Core Component Ball Mill Spare Parts
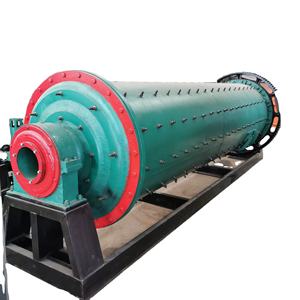
Ball mill spare parts Ball mill ring gear and gears Ball mill Gears
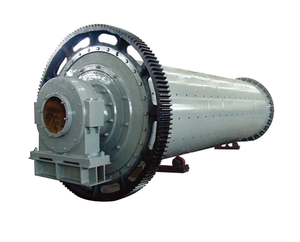
Mining Equipment Parts Ball Mill Machine Mining Equipment Sand Making Machine Ball Grinding Mill Liner Spare Parts
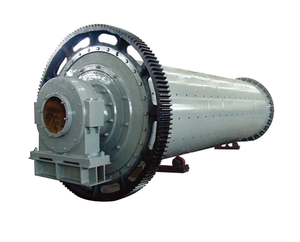