PRODUCT PARAMETERS
Description
Brief introduction of Ball Mill Working Principle, Milling Machine Tube, Overflow Ball Mill
Ball mill is a kind of equipment used to crush or grind materials to very fine powder, which is widely used in mining, cement, chemical industry, etc. Ball Mill Working Principle, Milling Machine Tube, Overflow Ball Mill refers to all kinds of parts and components which are necessary to ensure the normal operation of the ball mill, including liner plate, grinding balls, gears, bearings and so on.
Features and advantages of Ball Mill Working Principle, Milling Machine Tube, Overflow Ball Mill
Strong durability: Made of high-quality materials and under strict quality control, it ensures high wear resistance and long service life of spare parts.
Good interchangeability: The standardized design makes the spare parts interchangeable between different types of ball mills, simplifying the maintenance process.
Optimized design: Customised design according to the actual working conditions, which improves the working efficiency and reduces energy consumption at the same time.
Easy to install and maintain: reasonable structure, convenient for users to quickly replace and repair, reduce downtime.
Stable performance: Precision machining and rigorous testing ensure stable performance even in harsh environments.
(Ball Mill Working Principle, Milling Machine Tube, Overflow Ball Mill)
Specification of Ball Mill Working Principle, Milling Machine Tube, Overflow Ball Mill
A sphere mill is a vital commercial equipment utilized to grind materials right into great powders, critical in mineral handling, concrete manufacturing, and chemical industries. Its working principle focuses on rotation-induced impact and abrasion. The mill consists of a hollow cylindrical shell revolving around its straight axis. When the covering revolves, the grinding media (steel or ceramic spheres) and the raw material are lifted to a certain elevation before cascading down, developing a combination of impact pressures (from dropping rounds) and attrition (particle-on-particle rubbing). This double action efficiently damages down the product right into smaller sized bits. The rotational speed is crucial– too reduced, and balls slide without grinding; too expensive, and centrifugal force stops cascading, minimizing performance. Optimum operation happens at 60– 80% of the crucial rate (the speed at which centrifugal pressure amounts to gravity).
The milling machine tube, the core part, is a robust cylindrical chamber constructed from thick steel, lined with exchangeable abrasion-resistant products like manganese steel or rubber. Its length-to-diameter proportion determines grinding effectiveness: longer tubes allow finer grinding through extended material retention. The tube’s interior frequently features lifters or grooves to boost media movement. For wet grinding, slurry is fed and released with hollow trunnions; dry mills use diaphragms to control bit size.
An overflow ball mill is a kind of damp grinding mill where ground material departures using a discharge trunnion once the slurry level surpasses the overflow limit. This design makes certain constant procedure without external classifiers, perfect for great grinding in shut circuits. Overflow mills manage softer ores and create consistent bit dimensions but may need cyclones for size control. They are energy-efficient and low-maintenance, ideal for large procedures.
Trick requirements consist of capacity (ranging from lab-scale 5L mills to commercial 20,000 L units), motor power (5kW– 6,000 kW), rotational speed (12– 35 RPM), and feed/discharge dimension (as much as 25mm feed, 10– 300µm product). Liners and grinding media materials differ based upon application (e.g., stainless-steel for deterioration resistance). Overflow mills typically feature bigger diameters about length for optimal slurry circulation. Advanced designs include temperature level control systems and automated monitoring for procedure optimization.
(Ball Mill Working Principle, Milling Machine Tube, Overflow Ball Mill)
Applications of Ball Mill Working Principle, Milling Machine Tube, Overflow Ball Mill
The sphere mill functioning concept focuses on the turning of a hollow cyndrical tube loaded with grinding media, normally steel spheres. As the cyndrical tube turns, the balls are lifted to a specific height before plunging or dropping back down, influencing and grinding the material inside. This combination of effect and attrition lowers particle size, making ball mills essential for grinding and mixing materials in markets such as mining, concrete, ceramics, and chemicals. The process is very effective for both damp and completely dry grinding, providing versatility in processing ores, basic materials, and industrial powders.
The milling equipment tube, or the cylindrical covering, is a crucial part of the round mill. Its rotational rate figures out the effectiveness of the grinding process. At optimum rates, the rounds waterfall evenly, ensuring constant grinding. If the tube rotates too slowly, the rounds slide without adequate impact; if as well fast, centrifugal force keeps the rounds pinned to the walls, reducing efficiency. The tube’s length-to-diameter ratio additionally affects item fineness, with longer tubes making it possible for finer grinding. Its durable building and construction guarantees resilience under heavy tons and rough problems, making it ideal for continual procedure in rough settings.
Overflow round mills are a certain kind created to discharge ground material via the hollow trunnion once the slurry level surpasses the discharge opening. This layout prevents overgrinding and is optimal for coarse to medium particle dimension reduction. Frequently utilized in mineral handling, overflow sphere mills take care of products like gold, copper, and iron ore. Their simpleness in layout lowers upkeep expenses, while the consistent overflow discharge guarantees consistent product top quality. These mills are favored in closed-circuit grinding systems, where they function along with classifiers to achieve exact fragment dimension circulation.
Applications of these systems cover industries. In mining, they grind ores for more processing. Concrete plants use them to grate clinker, while ceramics rely upon round mills for great clay prep work. Overflow sphere mills are particularly effective in situations requiring gentle grinding without too much heat generation. Their versatility, efficiency, and dependability make them important in attaining consistent product uniformity, driving productivity throughout worldwide commercial operations.
Company Introduction
Established in 2007, Excavator Attachments Heavy Machinery Co.,ltd. focus on metal research and mining machinery spare parts. 2 factories over an area of 13,300 square meters, based on 100+ sets of equipment, our production capacity reaches 12000 Tons/Year. has passed ISO 9001 quality managment system certification in 2008.
Our mainly products are dragline excavator spare parts,rotary kiln spare parts, large modulus gear (gear shaft), gearbox ect. 40+ patents with over 45 years experience to help focus on improve the service life of spare parts. We belive that more than 80% reason of mechanical parts’ working life depends on hot processing (steel making/forging/casting/welding/heat treatment). Eight material engineers will control the quality from the original resource.
If you are interested, please feel free to contact us.
Payment
L/C, T/T, Western Union, Paypal, Credit Card etc.
Shipment
By sea, by air, by express, as customers request.
5 FAQs of Ball Mill Working Principle, Milling Machine Tube, Overflow Ball Mill
1. **How does a ball mill work?**
A ball mill operates by rotating a cylindrical shell around a horizontal axis, partially filled with grinding media like steel balls. As the mill rotates, the balls are lifted and dropped, crushing and grinding the material through impact and attrition. The material is fed into one end and discharged through the opposite end or peripherally, depending on the mill type, achieving a fine powder.
2. **What is the function of the milling machine tube in a ball mill?**
The milling machine tube (cylinder) houses the grinding media and raw material. It provides a controlled environment for rotation, ensuring consistent grinding by facilitating the tumbling motion of the balls. The tube’s length and diameter influence grinding efficiency, retention time, and product fineness, while its design prevents contamination and supports material flow from feed to discharge points.
3. **How does an overflow ball mill differ from a grate discharge ball mill?**
An overflow ball mill discharges ground material by overflow through a trunnion opening, ideal for fine grinding with a higher retention time. Grate discharge mills use a grate at the discharge end to separate grinding media from the product, allowing faster particle evacuation and coarser outputs. Overflow mills are simpler, while grate mills offer better control over particle size distribution.
4. **What factors influence the efficiency of a ball mill?**
Key factors include rotational speed (optimal speed ensures balls cascade effectively), grinding media size and material (affects impact force), feed rate and material hardness (influences grinding time), mill filling ratio (balance between media and material), and discharge design. Proper maintenance, lubrication, and alignment also prevent energy loss and wear.
5. **What are the primary advantages of using an overflow ball mill?**
Overflow ball mills are mechanically simple, cost-effective, and reliable. They handle both wet and dry grinding, produce uniform fine particles, and minimize overgrinding by allowing lighter particles to overflow. Their design reduces maintenance needs and accommodates varying feed sizes, making them suitable for industries like mining, ceramics, and chemicals requiring consistent fine grinding.
(Ball Mill Working Principle, Milling Machine Tube, Overflow Ball Mill)
REQUEST A QUOTE
RELATED PRODUCTS
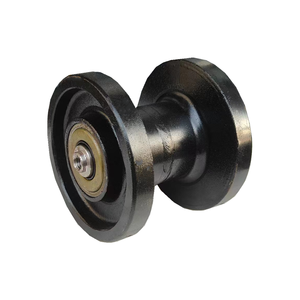
Gold Ore Iron Ore Grinding Machine Ball Mill Machine Dry Wet Type Ball mill s
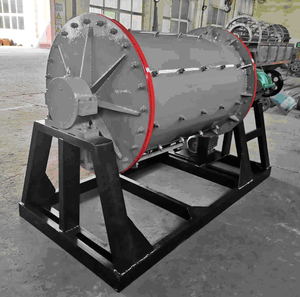
Gold Ore Lead Zinc Copper Mining Stone Mini Steel Coal Steel Used Wet Ball Mill and Dry Ball Mill for Mining Grinding
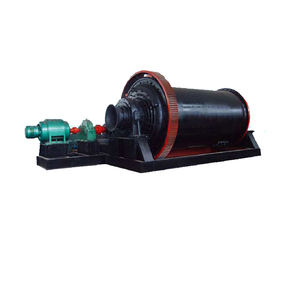
Large cement plant mill head rotary kiln spare parts welding ball mill welding drum
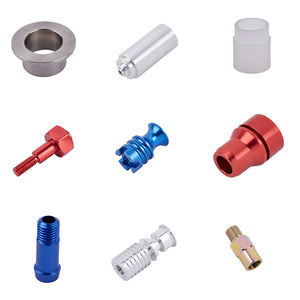
Factory Direct Supply High Quality ball mill with rubber liner ball mill
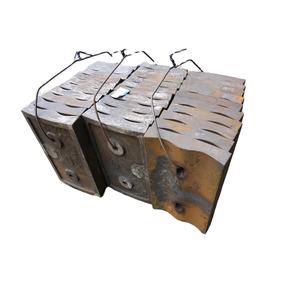
Horizontal PTFE Grinding Jars Ball Mill Parts Used For Laboratory Roller Milling Machine Alumina Grinding Jar Mill
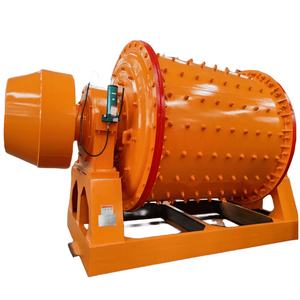