PRODUCT PARAMETERS
Description
Brief introduction of Factory Vertical Lead Oxide Aluminum Powder Ball Mill Ceramic Balls For Ball Mill
Ball mill is a kind of equipment used to crush or grind materials to very fine powder, which is widely used in mining, cement, chemical industry, etc. Factory Vertical Lead Oxide Aluminum Powder Ball Mill Ceramic Balls For Ball Mill refers to all kinds of parts and components which are necessary to ensure the normal operation of the ball mill, including liner plate, grinding balls, gears, bearings and so on.
Features and advantages of Factory Vertical Lead Oxide Aluminum Powder Ball Mill Ceramic Balls For Ball Mill
Strong durability: Made of high-quality materials and under strict quality control, it ensures high wear resistance and long service life of spare parts.
Good interchangeability: The standardized design makes the spare parts interchangeable between different types of ball mills, simplifying the maintenance process.
Optimized design: Customised design according to the actual working conditions, which improves the working efficiency and reduces energy consumption at the same time.
Easy to install and maintain: reasonable structure, convenient for users to quickly replace and repair, reduce downtime.
Stable performance: Precision machining and rigorous testing ensure stable performance even in harsh environments.
(Factory Vertical Lead Oxide Aluminum Powder Ball Mill Ceramic Balls For Ball Mill)
Specification of Factory Vertical Lead Oxide Aluminum Powder Ball Mill Ceramic Balls For Ball Mill
The Manufacturing Facility Upright Lead Oxide Light Weight Aluminum Powder Sphere Mill with Ceramic Spheres is a high-efficiency grinding maker designed for creating great powders of lead oxide and aluminum. Its upright framework optimizes space and makes certain consistent grinding. The mill utilizes resilient ceramic balls, decreasing contamination and wear, making it excellent for delicate materials. Trick specifications include a design number VM-500, a grinding capability of 1– 5 loads per hour, and a motor power of 15– 75 kW, adjustable based upon manufacturing needs. The turning rate ranges from 20– 40 RPM for accurate control over fragment dimension. Ceramic rounds are available in sizes of 10– 50 mm, crafted from high-purity alumina (Al ₂ O ₃) or zirconia (ZrO ₂), ensuring firmness (Mohs 9), rust resistance, and thermal security. The mill’s indoor features ceramic-lined chambers to stop steel contamination and improve sturdiness. It processes materials to a fineness of 10– 100 microns, suitable for battery production, pyrotechnics, and porcelains. The vertical design advertises power effectiveness, reducing power consumption by approximately 30% contrasted to horizontal mills. Safety attributes include overload defense, emergency stops, and secured chambers to prevent dirt leakage. The small dimensions (3– 5 meters in elevation, 2– 3 meters in impact) match manufacturing facility designs. Upkeep is minimal, with ceramic parts requiring replacement every 2,000– 3,000 hours of operation. Customizable choices include variable speed drives, automated feeding systems, and temperature level control. Compliance with ISO 9001 and ecological safety and security requirements makes certain dependability. Sound levels continue to be listed below 75 dB during procedure. The mill operates efficiently in temperature levels as much as 150 ° C and is compatible with completely dry and wet grinding techniques. A 12-month warranty covers manufacturing defects. Ideal for markets needing high-purity steel powders, this round mill combines efficiency, durability, and low contamination for regular performance.
(Factory Vertical Lead Oxide Aluminum Powder Ball Mill Ceramic Balls For Ball Mill)
Applications of Factory Vertical Lead Oxide Aluminum Powder Ball Mill Ceramic Balls For Ball Mill
Applications of Manufacturing Facility Upright Lead Oxide Aluminum Powder Ball Mill Porcelain Balls For Sphere Mill
Ceramic spheres are crucial grinding media in vertical round mills, especially for handling products like lead oxide and aluminum powder. Engineered for high-performance milling, these balls are crafted from sophisticated porcelains such as alumina (Al ₂ O ₃) or zirconia (ZrO ₂), making certain durability, chemical security, and resistance to put on. Their applications extend markets requiring fine, constant bit size circulation and contamination-free processing.
** Lead Oxide Processing: ** In lead-acid battery manufacturing, upright round mills grind lead oxide to specific specs. Ceramic spheres protect against metallic contamination, guaranteeing the oxide’s pureness for optimal battery performance. Their high density and firmness enable effective grinding without fracturing, maintaining procedure effectiveness and minimizing downtime.
** Aluminum Powder Manufacturing: ** Aluminum powder, made use of in pyrotechnics, aerospace, and metallurgy, needs ultra-fine milling with marginal oxidation threat. Ceramic balls’ non-sparking properties boost safety, while their thermal security handles exothermic responses during grinding. This guarantees constant fragment size and stops unwanted ignition risks.
** General Industrial Applications: ** Past specialized uses, ceramic balls are ideal for grinding abrasive or harsh materials in paints, coverings, and ceramics. Their inert nature avoids chemical reactions, protecting product integrity. Upright round mills gain from their uniform grinding activity, which improves energy effectiveness and reduces functional prices contrasted to typical steel media.
** Advantages of Ceramic Rounds: **.
– ** Wear Resistance: ** Outlast steel spheres, minimizing replacement regularity.
– ** Chemical Inertness: ** Perfect for responsive products like aluminum and lead compounds.
– ** Thermal Security: ** Withstand heats without breaking down.
– ** Contamination-Free Grinding: ** Make sure product purity in sensitive applications.
Readily available in sizes from 5mm to 50mm, these spheres accommodate diverse crushing requirements. Their smooth surface decreases rubbing, improving mill efficiency. By opting for ceramic grinding media, markets accomplish greater item quality, lower upkeep costs, and boosted process safety and security. Whether generating battery materials or sophisticated alloys, ceramic rounds in upright sphere mills provide precision, dependability, and lasting cost savings.
Company Introduction
Established in 2007, Excavator Attachments Heavy Machinery Co.,ltd. focus on metal research and mining machinery spare parts. 2 factories over an area of 13,300 square meters, based on 100+ sets of equipment, our production capacity reaches 12000 Tons/Year. has passed ISO 9001 quality managment system certification in 2008.
Our mainly products are dragline excavator spare parts,rotary kiln spare parts, large modulus gear (gear shaft), gearbox ect. 40+ patents with over 45 years experience to help focus on improve the service life of spare parts. We belive that more than 80% reason of mechanical parts’ working life depends on hot processing (steel making/forging/casting/welding/heat treatment). Eight material engineers will control the quality from the original resource.
If you are interested, please feel free to contact us.
Payment
L/C, T/T, Western Union, Paypal, Credit Card etc.
Shipment
By sea, by air, by express, as customers request.
5 FAQs of Factory Vertical Lead Oxide Aluminum Powder Ball Mill Ceramic Balls For Ball Mill
What are ceramic balls used for in vertical ball mills? Ceramic balls are grinding media designed for vertical ball mills to process materials like lead oxide and aluminum powder. They ensure efficient particle size reduction, uniform mixing, and consistent product quality. Their non-reactive nature prevents contamination, making them ideal for sensitive chemical applications where purity is critical.
Why choose ceramic balls over metal or other materials? Ceramic balls offer superior wear resistance, chemical stability, and thermal durability compared to metal alternatives. They do not corrode or react with abrasive materials like lead oxide or aluminum powder, ensuring a contamination-free grinding process. Their hardness and density enhance grinding efficiency while reducing energy consumption over time.
How do I maintain ceramic balls in a ball mill? Maintenance is minimal due to their durability. Regularly inspect the balls for cracks or excessive wear, and replace damaged ones to maintain grinding efficiency. Avoid abrupt temperature changes or mechanical impacts during operation. Clean the mill chamber periodically to remove residual powder, which can affect performance.
What advantages do ceramic balls offer over steel balls? Ceramic balls are non-contaminating, corrosion-resistant, and longer-lasting than steel balls. They generate less heat during grinding, preserving material properties. Their lightweight nature reduces energy consumption, and their wear resistance minimizes downtime for replacements, offering long-term cost savings.
Are ceramic balls compatible with all ball mills and materials? While optimized for vertical ball mills processing lead oxide or aluminum powder, ceramic balls can also function in horizontal mills. Compatibility depends on the mill’s operating parameters and material hardness. They are suitable for grinding non-ferrous metals, chemicals, and other materials requiring contamination-free processing. Always verify manufacturer specifications for your application.
(Factory Vertical Lead Oxide Aluminum Powder Ball Mill Ceramic Balls For Ball Mill)
REQUEST A QUOTE
RELATED PRODUCTS
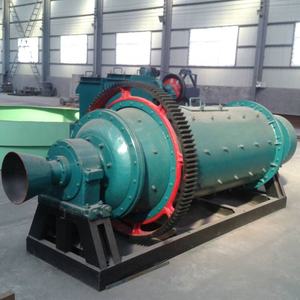
Cement Plant Large Diameter Zg35 Ball Mill Head Ball Mill End Cover

Portable high-performance ball mill spare parts 2 ton ball mill laboratory

Ball mill wear-resistant parts high chromium solid steel ball steel section cast alloy steel ball
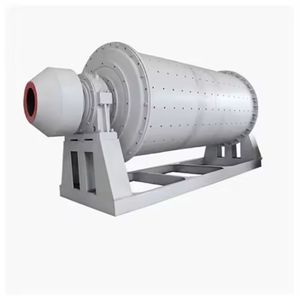
Customized Various Sizes Rotary Kiln Spare Parts Cement Ball Mill Drive Large Casting Gears
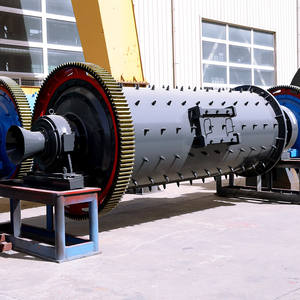
Rotary Kiln and Cement Ball Mill Spare Pasts Large Steel Spur Gear Wheel and Ring Gear Casting Girth Gear
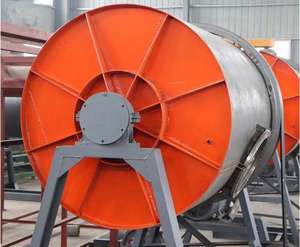