PRODUCT PARAMETERS
Description
Brief introduction of Electromagnetic vibrating feeder for feeder to ball mill from hopper
Ball mill is a kind of equipment used to crush or grind materials to very fine powder, which is widely used in mining, cement, chemical industry, etc. Electromagnetic vibrating feeder for feeder to ball mill from hopper refers to all kinds of parts and components which are necessary to ensure the normal operation of the ball mill, including liner plate, grinding balls, gears, bearings and so on.
Features and advantages of Electromagnetic vibrating feeder for feeder to ball mill from hopper
Strong durability: Made of high-quality materials and under strict quality control, it ensures high wear resistance and long service life of spare parts.
Good interchangeability: The standardized design makes the spare parts interchangeable between different types of ball mills, simplifying the maintenance process.
Optimized design: Customised design according to the actual working conditions, which improves the working efficiency and reduces energy consumption at the same time.
Easy to install and maintain: reasonable structure, convenient for users to quickly replace and repair, reduce downtime.
Stable performance: Precision machining and rigorous testing ensure stable performance even in harsh environments.
(Electromagnetic vibrating feeder for feeder to ball mill from hopper)
Specification of Electromagnetic vibrating feeder for feeder to ball mill from hopper
The Electromagnetic Vibrating Feeder is made to effectively and dependably transport bulk materials from a receptacle to a round mill in commercial handling applications. It makes use of electro-magnetic drive modern technology to generate regulated vibrations, making certain regular feed rates and very little material splilling. Secret specs include a robust steel building with a trough lined with wear-resistant material to handle abrasive compounds. The feeder operates a standard power supply of 220-440V A/C, 50/60Hz, with adjustable resonance strength by means of a variable voltage controller (0-100% modulation) to control product flow from 0.1 to 1500 lots per hour, depending upon the design and product thickness. The resonance frequency ranges between 3000 and 3600 resonances per min (50-60 Hz), enhanced for smooth, pulsation-free product discharge. The amplitude is adjustable from 0.5 mm to 3 mm to accommodate varying material dimensions and flow features. The trough dimensions are adjustable, with basic widths from 300 mm to 1500 mm and sizes as much as 2500 mm, making certain compatibility with receptacle electrical outlets and sphere mill inlets. The electro-magnetic drive system consumes low power (normally 0.2-2.2 kW) and operates calmly, reducing energy prices and noise pollution. It includes IP65-rated security for dirt and wetness resistance, making certain sturdiness in extreme environments. The feeder consists of overload defense and thermal sensors to avoid coil burnout. Control choices include manual adjustment or assimilation with automated systems using 4-20 mA signals for real-time flow monitoring. Maintenance needs are marginal due to the lack of rotating parts, and all components are quickly obtainable for assessment. The device is compliant with international safety and security standards (CE, ISO) and is suitable for industries such as mining, concrete, and chemical processing. Personalized alternatives include heat-resistant coatings, explosion-proof designs, and specialized trough arrangements for sticky or granular products.
(Electromagnetic vibrating feeder for feeder to ball mill from hopper)
Applications of Electromagnetic vibrating feeder for feeder to ball mill from hopper
Electromagnetic vibrating feeders play an important role in material handling systems, specifically in applications involving the regulated feeding of bulk products from a hopper to a round mill. These feeders utilize electro-magnetic drives to generate high-frequency resonances, making it possible for precise and reliable product circulation law. Their style makes certain uniform discharge rates, which is crucial for enhancing the efficiency of sphere mills in grinding and processing procedures.
One essential application remains in the mining and mineral handling market, where electro-magnetic shaking feeders transfer raw or crushed ore from storage hoppers to sphere mills. The regulated feeding protects against straining or underloading the mill, maintaining constant grinding efficiency and item quality. By adjusting the vibration amplitude and regularity, operators can make improvements the feed price to match the mill’s capability, decreasing energy waste and endure grinding media.
In cement production, these feeders take care of materials like limestone, clinker, and additives, making certain a consistent supply to ball mills for pulverization. The feeders’ ability to manage abrasive and heavy-duty materials without blocking or deterioration makes them perfect for harsh commercial atmospheres. In addition, their encased design minimizes dirt exhausts, improving office safety and security and compliance with ecological regulations.
Electromagnetic vibrating feeders additionally master chemical and metallurgical processes, where exact dosing of powders or granular materials is crucial. Their quick action to manage signals allows real-time adjustments, synchronizing feed prices with downstream procedures. This decreases product waste and makes certain optimal mill throughput.
Secret advantages include reduced maintenance due to the absence of revolving parts, decreased energy intake contrasted to mechanical feeders, and compatibility with automation systems. Combination with sensors and PLCs makes it possible for remote surveillance and adaptive control, aligning with Market 4.0 standards.
On the whole, electromagnetic vibrating feeders enhance functional effectiveness, reduce downtime, and improve process integrity in ball mill applications. Their convenience in handling diverse products– from great powders to rugged aggregates– makes them indispensable in industries focusing on precision, sustainability, and cost-effectiveness in material processing.
Company Introduction
Established in 2007, Excavator Attachments Heavy Machinery Co.,ltd. focus on metal research and mining machinery spare parts. 2 factories over an area of 13,300 square meters, based on 100+ sets of equipment, our production capacity reaches 12000 Tons/Year. has passed ISO 9001 quality managment system certification in 2008.
Our mainly products are dragline excavator spare parts,rotary kiln spare parts, large modulus gear (gear shaft), gearbox ect. 40+ patents with over 45 years experience to help focus on improve the service life of spare parts. We belive that more than 80% reason of mechanical parts’ working life depends on hot processing (steel making/forging/casting/welding/heat treatment). Eight material engineers will control the quality from the original resource.
If you are interested, please feel free to contact us.
Payment
L/C, T/T, Western Union, Paypal, Credit Card etc.
Shipment
By sea, by air, by express, as customers request.
5 FAQs of Electromagnetic vibrating feeder for feeder to ball mill from hopper
1. **How does an electromagnetic vibrating feeder work to transport material from a hopper to a ball mill?**
An electromagnetic vibrating feeder uses an electromagnetic drive to generate high-frequency vibrations. These vibrations move materials along a trough or pan from the hopper to the ball mill. The electromagnetic coil energizes to create a pulsating force, causing the feeder tray to vibrate. This controlled vibration ensures a steady, adjustable flow of bulk material, optimizing the feeding process for the ball mill’s grinding efficiency.
2. **What maintenance is required for an electromagnetic vibrating feeder?**
Regular maintenance includes checking the integrity of the electromagnetic coil, inspecting springs or leaf suspensions for wear, and ensuring all bolts are tightened. Clean the feeder tray to prevent material buildup, and lubricate moving parts as per the manufacturer’s guidelines. Periodic checks of the control system for voltage consistency also help maintain performance and longevity.
3. **Can electromagnetic vibrating feeders handle different types of materials?**
Yes, these feeders are versatile and handle dry, free-flowing materials like granules, powders, and small aggregates. However, material properties such as moisture content, abrasiveness, or stickiness may affect performance. Customizable tray liners or coatings can be added to reduce wear or adhesion issues for challenging materials.
4. **How is the feed rate adjusted on an electromagnetic vibrating feeder?**
The feed rate is controlled by adjusting the vibration intensity (amplitude) and frequency via a variable voltage regulator or programmable controller. Increasing the amplitude or voltage boosts material flow, while reducing it slows the feed. This allows precise tuning to match the ball mill’s processing capacity.
5. **What safety features are included in electromagnetic vibrating feeders?**
Common safety features include overload protection to prevent coil burnout, dust-proof enclosures for electrical components, and heat-resistant materials for high-temperature environments. Emergency stop functions and vibration dampers may also be integrated to ensure stable operation. Always ensure the feeder is securely mounted and grounded to avoid operational hazards.
(Electromagnetic vibrating feeder for feeder to ball mill from hopper)
REQUEST A QUOTE
RELATED PRODUCTS
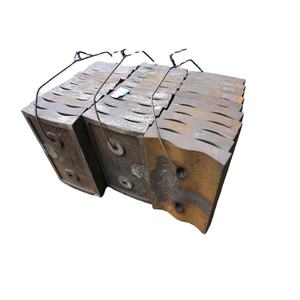
Ball Mill mining Equipment Accessories Hollow Shaft ball Mill Hollow Shaft For Material Feeding And Discharging
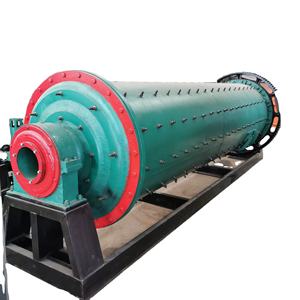
Rotary kiln and cement ball mill spare pasts wheel and ring gear casting girth gear large steel spur gear
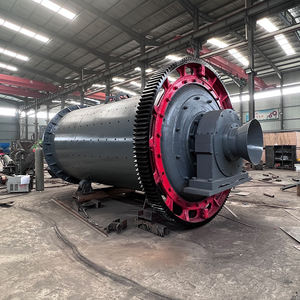
Casting Girth Gears Rotary Kiln And Cement Ball Mill Spare Parts Large Steel Spur Gear Wheel and Ring Gear
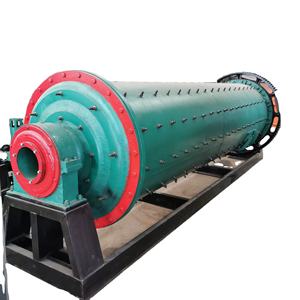
Ball mill spare parts Ball mill ring gear and gears Ball mill Gears
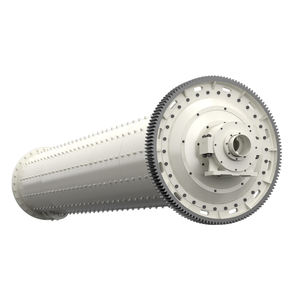
High Manganese Steel Alloy Chromium Wear Resistance Vertical Ball Mill Rubber Liner Plate Impact Crusher Wear Parts Liner
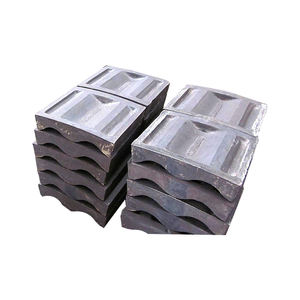