PRODUCT PARAMETERS
Description
Brief introduction of Ball Mill
Ball mill is a kind of equipment used to crush or grind materials to very fine powder, which is widely used in mining, cement, chemical industry, etc. Ball Mill refers to all kinds of parts and components which are necessary to ensure the normal operation of the ball mill, including liner plate, grinding balls, gears, bearings and so on.
Features and advantages of Ball Mill
Strong durability: Made of high-quality materials and under strict quality control, it ensures high wear resistance and long service life of spare parts.
Good interchangeability: The standardized design makes the spare parts interchangeable between different types of ball mills, simplifying the maintenance process.
Optimized design: Customised design according to the actual working conditions, which improves the working efficiency and reduces energy consumption at the same time.
Easy to install and maintain: reasonable structure, convenient for users to quickly replace and repair, reduce downtime.
Stable performance: Precision machining and rigorous testing ensure stable performance even in harsh environments.
(Ball Mill)
Specification of Ball Mill
A round mill is a cylindrical grinding device made use of to grind products right into great powders, important in markets such as mining, ceramics, cement, and chemicals. Secret specs consist of capacity, dimensions, rotation rate, grinding media, building products, power requirements, discharge systems, lining types, control systems, and safety features. Capability ranges from tiny research laboratory designs (5– 100 liters) to commercial devices exceeding 10,000 litres, refining a number of bunches per hour. Dimensions vary by application, with typical sizes of 1– 6 meters and sizes of 0.5– 3 meters, weighing from numerous kilos to over 100 heaps. Turning speed is crucial, operating at 65– 85% of the essential speed (calculated through √(g/(2πR)), where R is the drum distance), making sure optimum grinding effectiveness. Grinding media– steel, ceramic, or chrome rounds– range from 12– 50 mm in diameter, selected based on material solidity and fineness requirements. Round mills are built from abrasion-resistant materials like stainless-steel, carbon steel, or rubber-lined interiors for corrosion resistance. Motor power differs from 1 kW for laboratory units to over 1,000 kW for industrial mills, operating on 220V– 660V, with three-phase AC electric motors usual. Discharge kinds include grate (controlled particle dimension) and overflow (constant discharge), affecting output uniformity. Linings, made of manganese steel, rubber, or ceramic, secure the drum and boost grinding by decreasing wear. Advanced versions include automated control systems for speed, temperature level, and feed price, boosting accuracy. Safety and security systems include emergency stops, overload security, and confined layouts to reduce dust and noise. Ball mills handle materials like ores, pigments, and ceramics, producing fragments as great as 10 microns. Personalized choices consist of cooling coats, inert gas environments, and variable-speed drives. These specifications ensure versatility across industries, balancing effectiveness, toughness, and safety and security for diverse grinding needs.
(Ball Mill)
Applications of Ball Mill
A ball mill is a functional grinding maker extensively made use of throughout various sectors for grinding, mixing, and co-opting products. Its applications span from mining and building and construction to drugs and porcelains, making it important for material handling. Below are crucial applications of sphere mills:
** Mining and Metallurgy **: Round mills are essential in ore handling, grinding extracted materials like gold, copper, and iron ore into fine powders for further removal. They guarantee ideal particle dimension for reliable splitting up of metals from ores. In metallurgy, they refine steel powders for alloys and compounds, making sure harmony in buildings.
** Construction Products **: In cement manufacturing, ball mills grind basic materials like sedimentary rock, clay, and plaster into a fine powder (raw meal) before kiln processing. They likewise grate clinker to generate concrete, changing fineness to satisfy sector requirements. Furthermore, ball mills are utilized in producing ceramic tiles, grinding silica, feldspar, and various other raw materials to accurate uniformities.
** Chemicals and Paints **: Sphere mills grind pigments, materials, and additives to sub-micron degrees in paint and coating production, making certain smooth structures and constant color diffusion. In the chemical market, they mix reactive compounds and reduce bit size for drivers or plant foods, enhancing item efficiency.
** Pharmaceuticals **: Ball mills pulverize energetic pharmaceutical components (APIs) and excipients to improve medication dissolution rates and bioavailability. Their closed-system layout avoids contamination, crucial for meeting rigid health and wellness laws.
** Food Handling **: Though less usual, sphere mills grind food products like cacao or flavors right into ultra-fine powders, improving flavor release and texture. They are created with food-grade products to make certain safety and security.
** Environmental Applications **: Round mills reuse digital waste, grinding components to recover metals. They likewise process industrial waste right into recyclable products, sustaining lasting practices.
** R & d **: Laboratories usage small-scale sphere mills for product testing, nanoparticle synthesis, and explore grinding techniques for brand-new items.
Ball mills are valued for their versatility, dealing with completely dry or damp grinding, continual or set operations, and varied material types. Their effectiveness in reducing bit dimension and accomplishing homogeneity makes them vital in modern-day manufacturing. With adjustable liners, grinding media, and rate setups, ball mills provide tailored services across markets, driving advancement and performance.
Company Introduction
Established in 2007, Excavator Attachments Heavy Machinery Co.,ltd. focus on metal research and mining machinery spare parts. 2 factories over an area of 13,300 square meters, based on 100+ sets of equipment, our production capacity reaches 12000 Tons/Year. has passed ISO 9001 quality managment system certification in 2008.
Our mainly products are dragline excavator spare parts,rotary kiln spare parts, large modulus gear (gear shaft), gearbox ect. 40+ patents with over 45 years experience to help focus on improve the service life of spare parts. We belive that more than 80% reason of mechanical parts’ working life depends on hot processing (steel making/forging/casting/welding/heat treatment). Eight material engineers will control the quality from the original resource.
If you are interested, please feel free to contact us.
Payment
L/C, T/T, Western Union, Paypal, Credit Card etc.
Shipment
By sea, by air, by express, as customers request.
5 FAQs of Ball Mill
A ball mill is a key piece of equipment for grinding crushed materials into fine powder. Here are five frequently asked questions about ball mills and their answers:
**1. What is a ball mill used for?**
A ball mill is primarily used to grind materials such as ores, ceramics, chemicals, and paints into fine powder or slurry. It operates by rotating a cylinder filled with grinding media (steel or ceramic balls), which crushes and mixes materials through impact and attrition. Industries like mining, cement, and pharmaceuticals rely on ball mills for particle size reduction and homogenization.
**2. How does a ball mill work?**
The ball mill works by rotating a cylindrical shell around a horizontal axis. The grinding media inside the cylinder collide with the material, breaking it down through impact and friction. The rotation speed is critical—too slow, and the balls won’t cascade effectively; too fast, and centrifugal force prevents grinding. Material is fed into one end and discharged through the other, often with adjustable fineness.
**3. What materials can be processed in a ball mill?**
Ball mills handle a variety of materials, including hard minerals (like quartz and metals), soft minerals (like limestone), ceramics, and even organic materials. Wet or dry grinding is possible, depending on the material’s properties and the desired output. Abrasive or corrosive materials may require specialized linings or grinding media to prevent contamination or wear.
**4. How often should a ball mill be maintained?**
Regular maintenance is essential. Inspect liners, gears, and bearings every 250–300 hours of operation. Lubricate moving parts as per manufacturer guidelines. Replace worn grinding media and check seals for leaks. Overheating or unusual noises indicate immediate inspection. Preventive maintenance ensures efficiency, prolongs lifespan, and reduces downtime.
**5. What factors affect ball mill efficiency?**
Key factors include material hardness, feed size, mill speed, grinding media size and quantity, and discharge design. Optimal filling of grinding media (typically 30–40% of the mill volume) and correct rotational speed (65–80% of critical speed) maximize efficiency. Overloading or underloading the mill, improper ventilation, or using mismatched media sizes can reduce performance.
(Ball Mill)
REQUEST A QUOTE
RELATED PRODUCTS
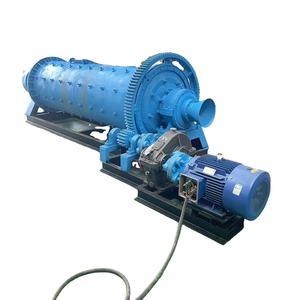
Custom Different Size End Cap Ball Mill Spare Parts Mining Machinery Ball Mill End Cover
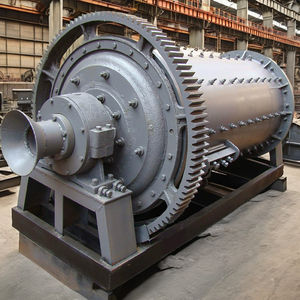
High crushing ratio 5 10 15 tons per hour cement mineral grinding ball mill with spare parts for gold silver copper crushing
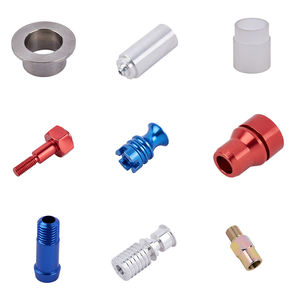
Effective Large Capacity Ball.Mill Ball Mill For Mining
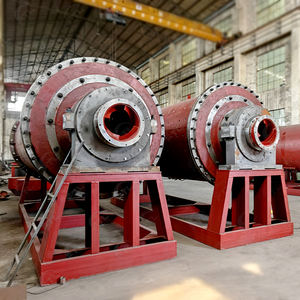
Mining energy ball mill metal matric ceramic parts ceramic table liner grinding roller
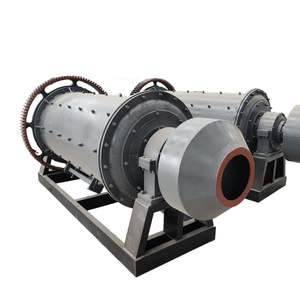
Source factory ball mill wear-resistant parts lining plate
