PRODUCT PARAMETERS
Description
Brief introduction of ball mill spare parts driving pinion / Ball Mill Pinion gear / lime kiln cement mill pinion for
Ball mill is a kind of equipment used to crush or grind materials to very fine powder, which is widely used in mining, cement, chemical industry, etc. ball mill spare parts driving pinion / Ball Mill Pinion gear / lime kiln cement mill pinion for refers to all kinds of parts and components which are necessary to ensure the normal operation of the ball mill, including liner plate, grinding balls, gears, bearings and so on.
Features and advantages of ball mill spare parts driving pinion / Ball Mill Pinion gear / lime kiln cement mill pinion for
Strong durability: Made of high-quality materials and under strict quality control, it ensures high wear resistance and long service life of spare parts.
Good interchangeability: The standardized design makes the spare parts interchangeable between different types of ball mills, simplifying the maintenance process.
Optimized design: Customised design according to the actual working conditions, which improves the working efficiency and reduces energy consumption at the same time.
Easy to install and maintain: reasonable structure, convenient for users to quickly replace and repair, reduce downtime.
Stable performance: Precision machining and rigorous testing ensure stable performance even in harsh environments.
(ball mill spare parts driving pinion / Ball Mill Pinion gear / lime kiln cement mill pinion for )
Specification of ball mill spare parts driving pinion / Ball Mill Pinion gear / lime kiln cement mill pinion for
The driving pinion, round mill pinion equipment, and lime kiln concrete mill pinion are crucial elements in industrial grinding and refining systems, created to transfer power successfully while withstanding heavy tons and harsh operating conditions. These equipments are precision-engineered to fit together flawlessly with bigger ring gears, guaranteeing smooth turning of sphere mills, concrete mills, and lime kilns. Secret specifications include material composition, dimensional precision, tons capacity, and resilience.
** Material: ** State-of-the-art alloy steels such as 42CrMo, 20MnCr5, or ASTM A48 are generally made use of for their exceptional stamina, wear resistance, and fatigue endurance. Heat therapy procedures like carburizing, relieving, and tempering enhance surface area hardness (approximately HRC 58-62) while maintaining a challenging core. Advanced surface treatments, consisting of nitriding or nickel-chrome plating, further enhance corrosion and abrasion resistance.
** Layout: ** Pinions include precision-machined helical or spur teeth with involute profiles to lessen friction and sound. Tooth modules range from 10 to 32, with pressure angles of 20 ° or 25 °, customized to match the ring gear. Customizable measurements (shaft diameter, face size, pitch size) guarantee compatibility with certain mill versions.
** Load Capability: ** Made to deal with high torque (as much as 150,000 Nm) and rotational rates (50-150 RPM), these gears go through strenuous testing to hold up against dynamic pressures in grinding applications. Ball mill pinions focus on shock resistance, while lime kiln variations concentrate on thermal stability in high-temperature atmospheres.
** Longevity: ** Lifespan goes beyond 5-7 years under optimal conditions, subject to proper lubrication (ISO VG 220-460 oils) and alignment. Regular assessments for wear, pitting, or misalignment are critical.
** Applications: ** Ball mill pinions drive grinding media for product pulverization in mining and concrete plants. Lime kiln pinions sustain calcination procedures, requiring resistance to warm and chemical exposure. Cement mill variants take care of clinker grinding with high dirt resistance.
** Personalization: ** OEM and aftermarket choices are available, with CAD/CAM-engineered designs to match gear proportions, shaft arrangements, and mounting demands. Conformity with ISO, AGMA, or racket criteria makes sure dependability.
These pinion gears are important for reducing downtime and optimizing functional efficiency in hefty sectors. Appropriate maintenance, including positioning checks and lubrication, makes sure peak performance and durability.
(ball mill spare parts driving pinion / Ball Mill Pinion gear / lime kiln cement mill pinion for )
Applications of ball mill spare parts driving pinion / Ball Mill Pinion gear / lime kiln cement mill pinion for
Round mill extra components such as driving pinions, sphere mill pinion gears, and lime kiln concrete mill pinions are essential components in durable industrial machinery, guaranteeing effective procedure across markets like cement production, mining, metallurgy, and chemical handling. These parts play a crucial role in transferring power, preserving rotational speed, and making it possible for the grinding or processing of basic materials.
** Driving Pinion Applications **: The driving pinion is a tiny gear that meshes with the bigger girth equipment on a sphere mill or rotary kiln, converting electric motor power into rotational activity. In concrete plants, it drives round mills utilized for grinding clinker, gypsum, and ingredients into fine concrete powder. Mining operations depend on driving pinions in ball mills to grate ores for mineral removal. Their robust design ensures durability under hefty lots and constant operation, decreasing downtime.
** Round Mill Pinion Equipment Applications **: Ball mill pinion gears work in tandem with girth equipments to rotate the mill drum, facilitating the grinding of materials like sedimentary rock, coal, and metal ores. These equipments are engineered for high torque transmission and accurate placement, critical in sectors calling for uniform fragment size circulation, such as porcelains or drugs. Heat-treated alloy steel building improves wear resistance, expanding life span also in rough settings.
** Lime Kiln Concrete Mill Pinion Applications **: In lime kilns and concrete mills, pinion gears drive rotary kilns during the calcination of limestone into quicklime or the sintering of concrete clinker. These components hold up against severe temperature levels and mechanical tension, making certain stable kiln turning for regular product top quality. Their accuracy machining minimizes vibration and sound, enhancing energy efficiency in high-temperature processing.
All three parts are vital for keeping functional connection. Personalized to match gear ratios and equipment requirements, they are frequently customized for specific tons abilities and environmental conditions. Normal upkeep of these pinions– such as lubrication and alignment checks– is vital to prevent unforeseen failings. By selecting high-grade spare components made from sturdy products like forged steel or alloy composites, markets improve performance, lower upkeep prices, and lengthen tools life-span. Whether in cement manufacturing, mineral handling, or lime manufacturing, these pinions make sure reliable power transmission, sustaining the backbone of industrial grinding and thermal handling systems.
Company Introduction
Established in 2007, Excavator Attachments Heavy Machinery Co.,ltd. focus on metal research and mining machinery spare parts. 2 factories over an area of 13,300 square meters, based on 100+ sets of equipment, our production capacity reaches 12000 Tons/Year. has passed ISO 9001 quality managment system certification in 2008.
Our mainly products are dragline excavator spare parts,rotary kiln spare parts, large modulus gear (gear shaft), gearbox ect. 40+ patents with over 45 years experience to help focus on improve the service life of spare parts. We belive that more than 80% reason of mechanical parts’ working life depends on hot processing (steel making/forging/casting/welding/heat treatment). Eight material engineers will control the quality from the original resource.
If you are interested, please feel free to contact us.
Payment
L/C, T/T, Western Union, Paypal, Credit Card etc.
Shipment
By sea, by air, by express, as customers request.
5 FAQs of ball mill spare parts driving pinion / Ball Mill Pinion gear / lime kiln cement mill pinion for
What is the purpose of a ball mill pinion gear? The pinion gear is a critical component in ball mills and rotary equipment like lime kilns or cement mills. It transfers rotational force from the motor to the mill’s girth gear, enabling the grinding or processing of materials. Properly functioning pinion gears ensure smooth torque transmission, minimize energy loss, and maintain operational efficiency. They are designed to mesh precisely with the larger girth gear, creating the rotational motion needed to drive the mill drum.
What are common signs of pinion gear wear or failure? Uneven noise during operation, such as grinding or clicking sounds, often indicates misalignment or tooth damage. Vibration, overheating, or visible pitting, cracks, or chipping on gear teeth are red flags. Reduced mill performance, like inconsistent grinding output or increased power consumption, may also signal pinion issues. Regular inspections and lubrication checks help detect early wear to prevent unplanned downtime.
What materials are pinion gears made of? High-quality pinion gears are forged from durable alloys like high-carbon steel, chromium-molybdenum steel, or nickel-chrome alloys. These materials provide high hardness, wear resistance, and load-bearing capacity. Heat treatment processes, such as carburizing or quenching, further enhance surface hardness and core toughness, ensuring longevity even under heavy-duty conditions in abrasive environments like cement plants.
How is pinion gear alignment checked and corrected? Precise alignment between the pinion and girth gear is crucial. Technicians use laser alignment tools or dial gauges to measure backlash, gear mesh clearance, and tooth contact patterns. Misalignment is corrected by adjusting the motor or gearbox position, shimming the base, or realigning couplings. Improper alignment accelerates wear, increases vibration, and risks catastrophic gear failure, so professional calibration during installation or maintenance is recommended.
How can I extend the lifespan of a ball mill pinion gear? Regular lubrication with high-viscosity industrial grease reduces friction and heat buildup. Monitor lubricant quality and avoid contamination. Conduct routine visual inspections for cracks, wear, or corrosion. Maintain proper alignment and avoid overloading the mill. Replace worn gears promptly to prevent secondary damage to the girth gear or drive system. Using OEM or precision-engineered replacement parts ensures compatibility and optimal performance.
(ball mill spare parts driving pinion / Ball Mill Pinion gear / lime kiln cement mill pinion for )
REQUEST A QUOTE
RELATED PRODUCTS
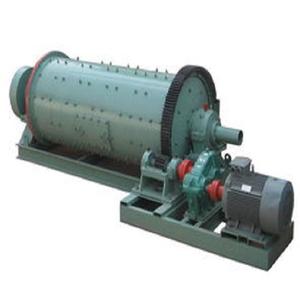
Small 5t/h ball mill for gold mining cement clinker grind ball mill limestone
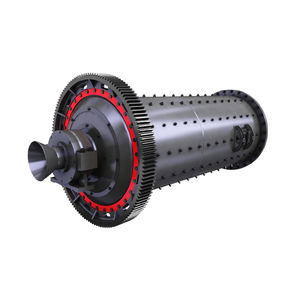
Ball mill spare parts Ball mill liners Ball mill liner
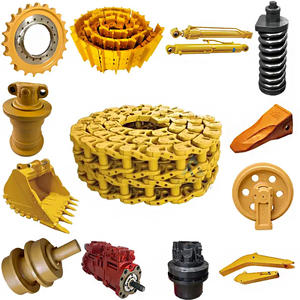
Ball mill Spare parts ball mill liner accessories ball mill liner plate
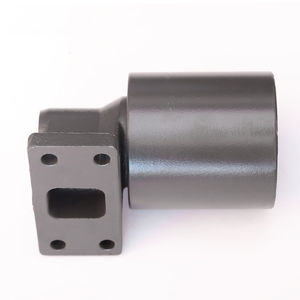
Metal Mine Ball Mill Liner Plate for Mining Machine Parts
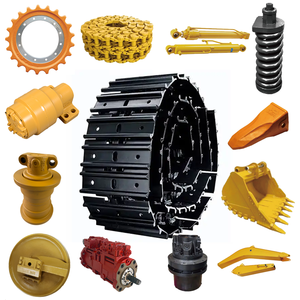
Large big 100 kg 900×3000 portable diesel engine ball mill parts for gold mining
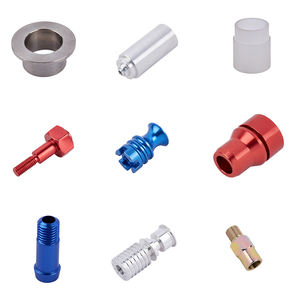