PRODUCT PARAMETERS
Description
Introduction to towed Excavator Hydraulic Breaker Ear Plates Head Top Brackets
A towed excavator, also known as a tracked or tire mobile excavator, is a type of heavy equipment that is widely used in the construction and mining sectors.Excavator Hydraulic Breaker Ear Plates Head Top Brackets refers to a variety of parts that are used to maintain, repair, or replace worn-out parts of this machine.
Features and advantages of towed Excavator Hydraulic Breaker Ear Plates Head Top Brackets
Durability: made of high-quality materials to ensure long life and high durability.
Compatibility: Designed to meet OEM specifications for a wide range of makes and models.
Economical: Third-party spare parts are usually less expensive compared to OEM parts.
Ease of Replacement: Standardised design allows for quick and easy installation and replacement.
Reliability: rigorously tested to ensure stable and reliable performance.
(Excavator Hydraulic Breaker Ear Plates Head Top Brackets)
Specification of Excavator Hydraulic Breaker Ear Plates Head Top Brackets
The Excavator Hydraulic Breaker Ear Plates, Head, and Leading Brackets are essential components developed to secure hydraulic breakers to excavator arms, ensuring security and reliable power transmission during demolition, mining, and construction procedures. These components are crafted to stand up to high-impact pressures, reduce vibration, and lengthen the lifespan of both the breaker and excavator.
** Material & Construction **: Manufactured from high-tensile alloy steel (Grade Q345B or matching), these parts are heat-treated for enhanced longevity, supplying remarkable resistance to wear, contortion, and tiredness. Crucial stress areas are strengthened to deal with repeated influence tons up to 10,000 N · m.
** Compatibility **: Developed to fit excavators varying from 1-ton to 50-ton classes, the braces are compatible with a lot of hydraulic breaker brand names (e.g., Atlas Copco, Montabert, NPK). Personalized measurements guarantee exact positioning– ear plate density (20– 50 mm), head size (150– 300 mm), and bracket height (200– 500 mm)– to match particular excavator and breaker models.
** Tons Ability **: Ranked for operating stress of 100– 250 bar, the brackets disperse mechanical tension evenly, reducing peak lots on the excavator’s arm. Optimum torque resistance is 1,500 N · m, with a temperature level tolerance variety of -30 ° C to
120 ° C. ** Surface Therapy **: Shot-blasted and coated with anti-corrosion epoxy or zinc plating to resist corrosion, abrasion, and rough ecological conditions. Precision-machined bolt holes guarantee safe and secure accessory, with ISO-standard threading (M20– M36) for compatibility with OEM hardware.
** Setup & Upkeep **: Pre-drilled openings and laser-cut layouts make it possible for quick installment. Normal evaluation for splits, screw tightness (suggested torque: 450– 600 N · m), and lubrication of pivot points are encouraged. Replace used components right away to avoid equipment damages.
** Certifications **: Compliant with ISO 9001 and CE standards, making sure reliability and safety. A 12-month warranty covers production issues. Personalized designs (e.g., prolonged brackets, solidified pins) are offered for specialized applications.
These parts maximize hydraulic breaker efficiency, decrease downtime, and enhance operational safety by keeping architectural honesty under extreme conditions. Ideal for durable applications in rock breaking, trenching, and concrete demolition.
(Excavator Hydraulic Breaker Ear Plates Head Top Brackets)
Applications of Excavator Hydraulic Breaker Ear Plates Head Top Brackets
Excavator hydraulic breaker ear plates, head, and leading brackets are vital elements designed to improve the performance, security, and sturdiness of hydraulic breakers utilized in construction, demolition, mining, and earthmoving applications. These parts collaborate to safeguard the hydraulic breaker to the excavator’s arm, making certain optimal power transfer and stability throughout high-impact procedures.
** Ear layers ** work as placing factors, attaching the breaker to the excavator’s boom. They absorb and disperse the intense vibrations created throughout rock breaking, concrete demolition, or trenching, decreasing tension on the device’s structure. Durable ear plates are essential for preserving placement and protecting against endure pivot pins, specifically in sturdy jobs like quarrying or roadway construction.
The ** head ** of the hydraulic breaker acts as the user interface between the tool (chisel or moil factor) and the excavator. It routes hydraulic stress to provide specific, powerful blows, making it suitable for fracturing tough surfaces, breaking boulders, or taking apart frameworks. A well-engineered head ensures constant performance, lessens energy loss, and extends the lifespan of the breaker by standing up to deformation under extreme loads.
** Top braces ** provide extra assistance by supporting the breaker’s top section. They avoid side movement throughout procedure, which is essential when working on unequal terrain or dealing with angled strikes. In applications like mining or tunneling, top braces help keep breaker placement, decreasing the danger of tool slippage and boosting operator security.
These elements are important in demanding environments where dependability is non-negotiable. For instance, in demolition tasks, they allow continual operation without frequent downtime for modifications. In landscaping or agricultural trenching, they make sure accuracy while decreasing wear on the excavator. Made from high-grade steel and heat-treated for durability, ear plates, heads, and leading braces resist abrasion, corrosion, and exhaustion, also in rough conditions.
By investing in quality hydraulic breaker components, operators boost job site efficiency, lower maintenance expenses, and extend devices durability. Their design guarantees compatibility with various excavator versions and breaker sizes, making them adaptable for varied jobs– from light urban demolition to hefty industrial rock splitting. Appropriate setup and regular inspection of these components even more enhance efficiency, making sure secure and efficient procedure across all applications.
Company Introduction
Established in 2007, Excavator Attachments Heavy Machinery Co.,ltd. focus on metal research and mining machinery spare parts. 2 factories over an area of 13,300 square meters, based on 100+ sets of equipment, our production capacity reaches 12000 Tons/Year. has passed ISO 9001 quality managment system certification in 2008.
Our mainly products are dragline excavator spare parts,rotary kiln spare parts, large modulus gear (gear shaft), gearbox ect. 40+ patents with over 45 years experience to help focus on improve the service life of spare parts. We belive that more than 80% reason of mechanical parts’ working life depends on hot processing (steel making/forging/casting/welding/heat treatment). Eight material engineers will control the quality from the original resource.
If you are interested, please feel free to contact us.
Payment
L/C, T/T, Western Union, Paypal, Credit Card etc.
Shipment
By sea, by air, by express, as customers request.
5 FAQs of Excavator Hydraulic Breaker Ear Plates Head Top Brackets
What are excavator hydraulic breaker ear plates and head top brackets? Excavator hydraulic breaker ear plates and head top brackets are critical components designed to secure the hydraulic breaker to the excavator’s arm. They absorb high-impact forces during demolition or rock-breaking operations, ensuring stability and alignment. Made from high-strength steel or alloy, these parts withstand extreme stress, reducing wear on the breaker and excavator.
How do I ensure proper installation of ear plates and head top brackets? Proper installation requires matching the brackets and ear plates to the excavator and breaker model specifications. Follow the manufacturer’s guidelines for torque settings, bolt alignment, and lubrication. Use genuine parts to avoid compatibility issues. Incorrect installation can lead to misalignment, excessive vibration, or component failure. If unsure, consult a certified technician.
What maintenance do these components require? Regular inspections are essential. Check for cracks, deformation, or wear on the ear plates and brackets after heavy use. Tighten loose bolts and lubricate pivot points to prevent rust and friction. Replace worn-out bushings or pins promptly. Neglecting maintenance can cause irreversible damage to the breaker or excavator arm, leading to costly repairs.
How long do hydraulic breaker ear plates and brackets last? Lifespan depends on operating conditions, material quality, and maintenance. High-quality components under moderate use may last 1–3 years. Heavy-duty applications in abrasive environments (e.g., mining) may require replacement every 6–12 months. Monitor performance for signs like excessive noise, reduced breaker efficiency, or visible damage to determine replacement timing.
Can I use generic ear plates and brackets instead of OEM parts? While generic parts may be cheaper, they often lack the precision engineering and durability of OEM (Original Equipment Manufacturer) components. Poorly fitting or low-strength alternatives risk premature failure, misalignment, and safety hazards. OEM parts ensure compatibility, optimal performance, and warranty coverage. Always verify specifications or consult your breaker manufacturer before purchasing non-OEM replacements.
(Excavator Hydraulic Breaker Ear Plates Head Top Brackets)
REQUEST A QUOTE
RELATED PRODUCTS
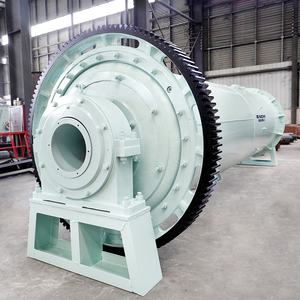
Hydraulic Parts TEIJIN M3V130 M3V270 Mini Excavator Final Drive Parts ravel Motor Spare Parts
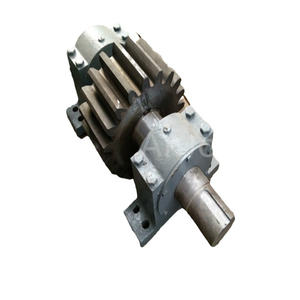
High Quality EX100 EX120 EX135 EX150 EX160 Hitachi Excavator Track Lower Roller Undercarriage Parts Track Roller
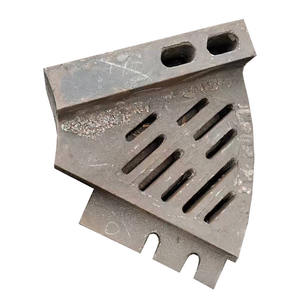
High Performance Joystick Controller with Encoder Competitive for Construction Machinery Parts Cranes Excavators
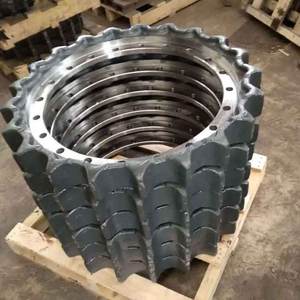
E10 Series Undercarriage Part Top Carrier Roller Idler Track Bottom Roller Drive Sprocket For Bobcat Mini Excavator Spare Parts
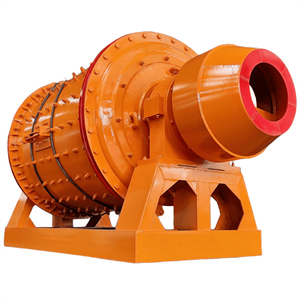
Mini Excavator Undercarriage Parts Rubber Track Assembly Front Idler Drive Sprocket Track Bottom Roller For Takeuchi
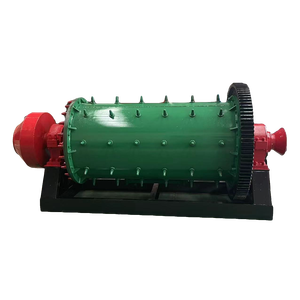