PRODUCT PARAMETERS
Description
Brief introduction of Ball Mill For Tiles Ball Mill For Mining Copper
Ball mill is a kind of equipment used to crush or grind materials to very fine powder, which is widely used in mining, cement, chemical industry, etc. Ball Mill For Tiles Ball Mill For Mining Copper refers to all kinds of parts and components which are necessary to ensure the normal operation of the ball mill, including liner plate, grinding balls, gears, bearings and so on.
Features and advantages of Ball Mill For Tiles Ball Mill For Mining Copper
Strong durability: Made of high-quality materials and under strict quality control, it ensures high wear resistance and long service life of spare parts.
Good interchangeability: The standardized design makes the spare parts interchangeable between different types of ball mills, simplifying the maintenance process.
Optimized design: Customised design according to the actual working conditions, which improves the working efficiency and reduces energy consumption at the same time.
Easy to install and maintain: reasonable structure, convenient for users to quickly replace and repair, reduce downtime.
Stable performance: Precision machining and rigorous testing ensure stable performance even in harsh environments.
(Ball Mill For Tiles Ball Mill For Mining Copper)
Specification of Ball Mill For Tiles Ball Mill For Mining Copper
The round mill for floor tiles and mining copper is constructed to handle hard grinding jobs. It works for both ceramic floor tile manufacturing and copper ore processing. The machine is made from solid steel plates. These plates are welded together for added toughness. The inner lining uses high manganese steel. This material withstands wear from constant grinding. The drum size varies. Common models have drums from 900 mm to 3500 mm in size. Bigger drums process extra material per hour.
The motor power varies in between 15 kW and 450 kW. This depends upon the drum size and workload. The electric motor drives a durable gearbox. The gearbox makes certain smooth turning of the drum. Rotation speed is adjustable. Operators regulate it based on product kind. Faster rates create finer fragments. Slower speeds are much better for rugged grinding.
Grinding media inside the drum are steel rounds. These balls be available in sizes from 25 mm to 75 mm. They squash raw materials right into powder. For copper mining, larger spheres damage tough ore initially. Smaller balls refine the bits later on. The round mill can stand up to 30 tons of grinding media. This depends upon the drum’s capacity.
Feed material gets in via a secured inlet. A conveyor system or hand-operated loading is feasible. The maximum feed size is 25 mm for copper ore. For ceramic floor tile products, it’s 20 mm. Release occurs with a screen at the drum’s end. Screen mesh sizes range from 200 to 500 microns. This regulates the final particle size.
The device includes safety and security attributes. An overload sensor stops the electric motor if stress gets too expensive. Emergency switches are put on all sides. Safety covers protect against contact with relocating parts. Upkeep is simple. Accessibility panels let employees inspect the drum without dismantling it. Lubrication factors are easy to reach.
Energy performance is a concern. The layout minimizes power usage by approximately 20% contrasted to older versions. Shielded electric motors prevent overheating. Sound degrees stay below 85 decibels throughout procedure. This fulfills workplace safety requirements.
Custom alternatives are offered. These consist of rubber linings for quieter grinding or ceramic cellular linings for floor tile manufacturing. Some designs add a water-cooling system for long runs. The round mill collaborates with damp or completely dry materials. This flexibility suits various industries.
The base framework uses strengthened steel beam of lights. This keeps the device stable during hefty use. Setup calls for a flat concrete foundation. Electrical wiring complies with global safety and security codes. Spare components like liners and gears are easy to change. Most components are standard sizes. This reduces downtime for fixings.
(Ball Mill For Tiles Ball Mill For Mining Copper)
Applications of Ball Mill For Tiles Ball Mill For Mining Copper
Round mills are very important machines in sectors such as ceramic tile manufacturing and copper mining. They grind materials right into fine powders. This process is required for making consistent items. In floor tile production, sphere mills crush basic materials like clay, feldspar, and quartz. These materials should be ground to a certain size. Uniform fragment size guarantees ceramic tiles have also appearance and toughness. Round mills blend materials thoroughly during grinding. This produces an uniform combination. The blend is after that formed and discharged into tiles. Without correct grinding, ceramic tiles might split or have weak points. Adjusting the mill’s rotation speed manages grinding efficiency. Faster speeds create finer fragments. Slower speeds conserve energy but produce coarser outcome. Operators equilibrium these factors for optimal results.
In copper mining, round mills break down ore removed from the ground. Copper ore is typically hard and mixed with various other rocks. Sphere mills crush the ore into little fragments. This exposes copper minerals for further handling. After grinding, the ore goes through flotation protection. Chemicals separate copper from waste material. Efficient grinding rises copper recuperation rates. Big mining operations make use of ball mills in continual cycles. This keeps handling constant and reduces downtime. Damp grinding prevails in mining. Water is added to the mill to create a slurry. Slurries move conveniently through processing stages. Dry grinding is made use of when moisture affects later on actions.
Ball mills for tiles and copper mining share basic designs. Both make use of revolving cylinders loaded with grinding media like steel rounds. The material is fed into the cyndrical tube. As it revolves, balls ram the product. Impact and rubbing break fragments apart. Lining the cylinder shields it from wear. Various linings suit various materials. Upkeep makes sure long service life. Routine checks stop unforeseen break downs. Correct lubrication maintains components moving efficiently.
Operators choose ball mill dimensions based on manufacturing demands. Little mills benefit laboratories or tiny factories. Big mills manage industrial-scale outcome. Power performance is a priority. More recent designs utilize much less power while maintaining performance. Personalization alternatives allow markets adapt mills to particular jobs. Flexible setups control fragment size and grinding speed. This flexibility makes ball mills flexible across applications.
Company Introduction
Established in 2007, Excavator Attachments Heavy Machinery Co.,ltd. focus on metal research and mining machinery spare parts. 2 factories over an area of 13,300 square meters, based on 100+ sets of equipment, our production capacity reaches 12000 Tons/Year. has passed ISO 9001 quality managment system certification in 2008.
Our mainly products are dragline excavator spare parts,rotary kiln spare parts, large modulus gear (gear shaft), gearbox ect. 40+ patents with over 45 years experience to help focus on improve the service life of spare parts. We belive that more than 80% reason of mechanical parts’ working life depends on hot processing (steel making/forging/casting/welding/heat treatment). Eight material engineers will control the quality from the original resource.
If you are interested, please feel free to contact us.
Payment
L/C, T/T, Western Union, Paypal, Credit Card etc.
Shipment
By sea, by air, by express, as customers request.
5 FAQs of Ball Mill For Tiles Ball Mill For Mining Copper
A ball mill grinds materials into fine powder. It is used in tile manufacturing and copper mining. The machine crushes raw materials for consistent texture in tiles. For copper, it breaks ore into smaller particles for further processing.
The ball mill works by rotating a drum with steel balls inside. Materials enter the drum. The balls hit and grind them as the drum spins. For tiles, this creates uniform ceramic powder. For copper, it prepares ore for chemical extraction. The process ensures efficient grinding for both applications.
Key features include a robust steel construction. It handles heavy loads during operation. Adjustable rotation speeds allow control over grinding fineness. Wear-resistant liners protect the drum from damage. These features make it reliable for tiles and mining. The design supports continuous use in demanding environments.
Regular maintenance is necessary. Check liners and grinding balls for wear. Replace them when worn out. Lubricate moving parts to reduce friction. Inspect bolts and seals to prevent leaks. Proper upkeep minimizes downtime. Maintenance routines are similar for tile and copper processing. This keeps the mill running efficiently.
A ball mill is cost-effective long-term. It reduces energy use compared to other grinders. Low maintenance cuts operational costs. High grinding efficiency speeds production. For tiles, it ensures quality with minimal waste. In copper mining, it improves recovery rates. The initial investment pays off through reliable performance.
(Ball Mill For Tiles Ball Mill For Mining Copper)
REQUEST A QUOTE
RELATED PRODUCTS
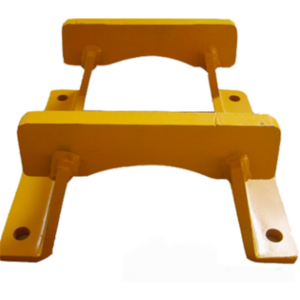
Lab Ball Mill Machine Mill Stone Gold Ore Ball Mill Liner Wear Plate Spare Parts
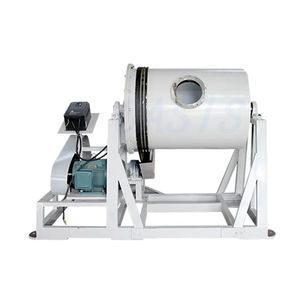
Manufacture super good quality Resistant Mining Spare Parts ball mill rubber lining
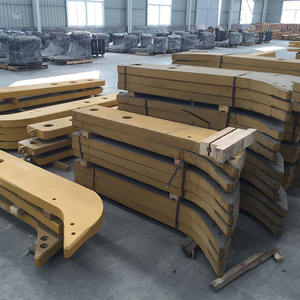
High Quality Forged Steel Balls and liners For Ball Mill, Attrition Mill
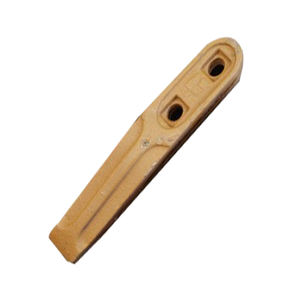
Customizable OEM Ball Mill Motor

Highly Demanded Item Year 2023 OEM Custom Cast Steel Liner Ball Mill Wear Resistant Part Cheap Cement Making Specialized Product
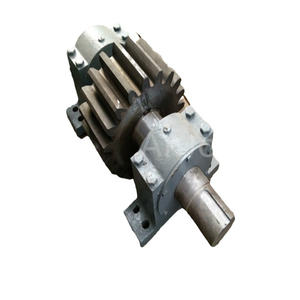