PRODUCT PARAMETERS
Description
Brief introduction of Ball Mill Liner Plate Lining For Mining Grinding Machine s lining of the ball mill
Ball mill is a kind of equipment used to crush or grind materials to very fine powder, which is widely used in mining, cement, chemical industry, etc. Ball Mill Liner Plate Lining For Mining Grinding Machine s lining of the ball mill refers to all kinds of parts and components which are necessary to ensure the normal operation of the ball mill, including liner plate, grinding balls, gears, bearings and so on.
Features and advantages of Ball Mill Liner Plate Lining For Mining Grinding Machine s lining of the ball mill
Strong durability: Made of high-quality materials and under strict quality control, it ensures high wear resistance and long service life of spare parts.
Good interchangeability: The standardized design makes the spare parts interchangeable between different types of ball mills, simplifying the maintenance process.
Optimized design: Customised design according to the actual working conditions, which improves the working efficiency and reduces energy consumption at the same time.
Easy to install and maintain: reasonable structure, convenient for users to quickly replace and repair, reduce downtime.
Stable performance: Precision machining and rigorous testing ensure stable performance even in harsh environments.
(Ball Mill Liner Plate Lining For Mining Grinding Machine s lining of the ball mill)
Specification of Ball Mill Liner Plate Lining For Mining Grinding Machine s lining of the ball mill
Round mill lining plates are essential parts made to shield the inner covering of the round mill from wear and tear caused by unpleasant products throughout the grinding process. These liners enhance grinding effectiveness, expand the mill’s life expectancy, and reduce maintenance expenses. Built from top notch products like high manganese steel, chromium alloy steel, or rubber, they are engineered to endure impact, abrasion, and corrosion in harsh mining atmospheres. The lining plates are customized to fit different mill types, consisting of cement mills, mining ball mills, and ore-processing mills, ensuring optimal efficiency throughout applications.
The key function of sphere mill linings is to protect the mill shell while lifting and plunging grinding media (rounds) to take full advantage of product dimension decrease. Linings come in numerous layouts, such as wave, rib, action, and ladder setups, each fit for details grinding problems. Wave liners are excellent for great grinding, while ribbed linings excel in rugged grinding by promoting much better media movement. Action liners boost grinding effectiveness by readjusting the trajectory of spheres, and ladder liners are used in secondary grinding chambers for regular performance.
Trick specs consist of density (30– 150 mm), solidity (HRC 50– 65 for steel alloys), and dimensions customized to mill size and length. High manganese steel linings offer remarkable effect resistance, while chromium alloy versions supply extended wear life in highly rough environments. Rubber linings are light-weight, lower sound, and are ideal for wet grinding. Liners are bolted or bonded to the mill covering, with lifter bars incorporated to maximize grinding media activity.
Applications cover gold, copper, iron ore, and concrete processing. Functions include resistance to thermal contortion, very easy setup, and compatibility with all ball mill kinds. Routine examination and replacement of worn liners prevent mill downtime and preserve grinding performance. Adjustable accounts and alloy structures ensure versatility to particular functional requirements, such as particle size needs or slurry problems.
In recap, round mill lining plates are crucial for efficient mineral handling, integrating durable materials, cutting-edge designs, and accurate design to deliver longevity and performance. They lessen functional prices by reducing endure grinding media and mill parts, making certain dependable operation in demanding mining and commercial environments.
(Ball Mill Liner Plate Lining For Mining Grinding Machine s lining of the ball mill)
Applications of Ball Mill Liner Plate Lining For Mining Grinding Machine s lining of the ball mill
Round mill lining plates are vital parts in mining grinding devices, designed to secure the mill’s internal shell and improve operational performance. These linings are indispensable to the grinding process, where ores and minerals are reduced to great fragments. Their primary application hinges on safeguarding the mill framework from the extreme abrasion, impact, and wear brought on by grinding media (steel or ceramic rounds) and resources. This security expands the mill’s life expectancy, decreasing maintenance expenses and downtime.
In mining operations, lining plates are tailored to manage diverse products, from difficult ores like gold, copper, and iron to softer minerals such as sedimentary rock or coal. High manganese steel, chromium alloys, and rubber are common materials made use of for linings, each offering one-of-a-kind benefits. Manganese steel linings excel in high-impact atmospheres, while rubber liners decrease sound and are excellent for wet grinding.
The style of liner plates directly effects grinding efficiency. Wave, stepped, or ribbed liners maximize the trajectory of grinding media, guaranteeing efficient fragment dimension decrease. Properly developed linings take full advantage of power transfer, improving throughput and lowering power usage. They additionally prevent material slippage, ensuring regular grinding performance.
Lining plates play an important role in cost-effectiveness. Durable liners reduce replacement frequency, lowering operational expenditures. Their ability to stand up to rough problems guarantees nonstop production, essential for large mining procedures. Additionally, advanced liner layouts decrease the danger of mill downtime because of unexpected wear or damage, boosting total performance.
Security is an additional vital application. By maintaining the architectural honesty of the mill, linings prevent tragic failings that can endanger employees. Rubber linings, for instance, deal rust resistance in acidic or wet settings, even more boosting safety and long life.
In summary, ball mill liner plates are essential for reliable, secure, and economical mineral processing. Their flexibility to different products, designs, and operational problems makes them essential in extracting grinding applications, making certain optimal performance and long life of grinding machinery.
Company Introduction
Established in 2007, Excavator Attachments Heavy Machinery Co.,ltd. focus on metal research and mining machinery spare parts. 2 factories over an area of 13,300 square meters, based on 100+ sets of equipment, our production capacity reaches 12000 Tons/Year. has passed ISO 9001 quality managment system certification in 2008.
Our mainly products are dragline excavator spare parts,rotary kiln spare parts, large modulus gear (gear shaft), gearbox ect. 40+ patents with over 45 years experience to help focus on improve the service life of spare parts. We belive that more than 80% reason of mechanical parts’ working life depends on hot processing (steel making/forging/casting/welding/heat treatment). Eight material engineers will control the quality from the original resource.
If you are interested, please feel free to contact us.
Payment
L/C, T/T, Western Union, Paypal, Credit Card etc.
Shipment
By sea, by air, by express, as customers request.
5 FAQs of Ball Mill Liner Plate Lining For Mining Grinding Machine s lining of the ball mill
What is the purpose of a ball mill liner plate?
Ball mill liner plates protect the inner shell of the grinding mill from wear caused by abrasive materials and grinding media. They also enhance grinding efficiency by optimizing the trajectory of grinding media (like steel balls) to ensure effective impact and friction for material size reduction. Properly designed liners reduce energy consumption and extend the mill’s operational lifespan.
What materials are used for ball mill liner plates?
Common materials include high manganese steel, chromium alloy steel, rubber, and composite materials. High manganese steel offers excellent impact resistance, while alloy steel provides hardness for abrasive environments. Rubber liners reduce noise and are ideal for wet grinding. Composite liners combine materials like steel and rubber to balance durability and energy efficiency. The choice depends on factors like material hardness, operating temperature, and corrosion risks.
How often should ball mill liner plates be replaced?
Replacement intervals vary based on material abrasiveness, mill speed, liner material, and operational hours. Typically, liners last between 6 to 12 months. Regular inspections are critical—replace liners when thickness reduces to 30–50% of the original or if cracks/deformation occur. Delaying replacement risks mill damage and inefficient grinding.
What factors affect the lifespan of ball mill liners?
Key factors include the hardness and size of processed materials, grinding media type, mill rotational speed, and operating conditions (e.g., wet vs. dry grinding). Improper loading, misalignment, or excessive mill vibration accelerate wear. Using mismatched liner materials for the application also shortens lifespan.
How to maintain ball mill liner plates?
Conduct routine visual and thickness inspections to detect early wear. Replace liners uniformly to avoid imbalance. Ensure proper alignment during installation and use grinding media of appropriate size and hardness. Avoid overloading the mill and monitor operational parameters like temperature and vibration. Clean the mill regularly to prevent material buildup, which can cause uneven wear. Proper maintenance minimizes downtime and optimizes grinding performance.
By addressing these FAQs, users can maximize liner plate efficiency, reduce maintenance costs, and ensure consistent grinding output in mining operations.
(Ball Mill Liner Plate Lining For Mining Grinding Machine s lining of the ball mill)
REQUEST A QUOTE
RELATED PRODUCTS
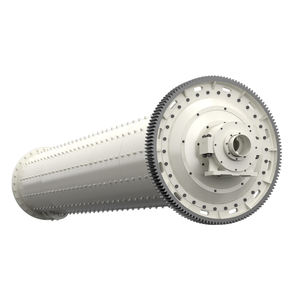
High Manganese Steel Alloy Chromium Wear Resistance Vertical Ball Mill Rubber Liner Plate Impact Crusher Wear Parts Liner
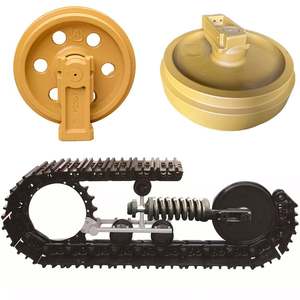
Iron Ore Ball Mills Gypsum Grinding Ball Mill Machine Gold Provided AC Motor Spare Part of Cement Factory Steel Ball Mill 1year
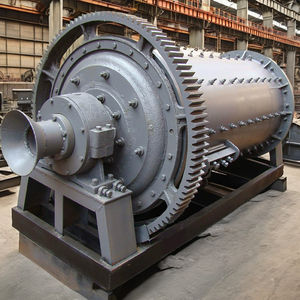
High crushing ratio 5 10 15 tons per hour cement mineral grinding ball mill with spare parts for gold silver copper crushing
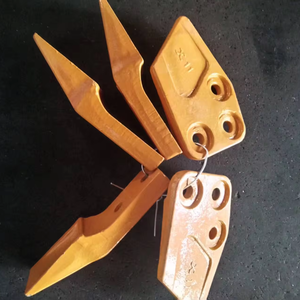
Ball Mill 6 Ball Mill Parts Gear Aluminum Powder Ball Mill 1200*4500
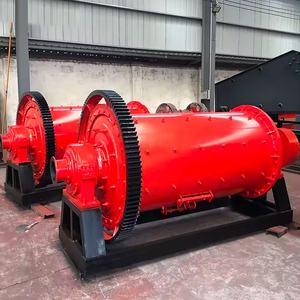
ball mill spare parts All Sizes Provided high manganese forged steel ball
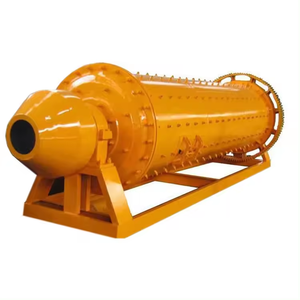