PRODUCT PARAMETERS
Description
Brief introduction of Ball mill Pinion Gear for Ball Mill
Ball mill is a kind of equipment used to crush or grind materials to very fine powder, which is widely used in mining, cement, chemical industry, etc. Ball mill Pinion Gear for Ball Mill refers to all kinds of parts and components which are necessary to ensure the normal operation of the ball mill, including liner plate, grinding balls, gears, bearings and so on.
Features and advantages of Ball mill Pinion Gear for Ball Mill
Strong durability: Made of high-quality materials and under strict quality control, it ensures high wear resistance and long service life of spare parts.
Good interchangeability: The standardized design makes the spare parts interchangeable between different types of ball mills, simplifying the maintenance process.
Optimized design: Customised design according to the actual working conditions, which improves the working efficiency and reduces energy consumption at the same time.
Easy to install and maintain: reasonable structure, convenient for users to quickly replace and repair, reduce downtime.
Stable performance: Precision machining and rigorous testing ensure stable performance even in harsh environments.
(Ball mill Pinion Gear for Ball Mill)
Specification of Ball mill Pinion Gear for Ball Mill
The Ball Mill Pinion Equipment is a crucial part in the operation of a sphere mill, created to transmit rotational activity and torque from the electric motor to the mill cyndrical tube, allowing the grinding procedure. Constructed from high-quality alloy steel, such as 4340 or comparable grades, the pinion gear goes through exact warm treatment processes like carburizing or induction solidifying to attain superior surface hardness (typically 58-62 HRC) and core durability (30-35 HRC). This makes certain remarkable wear resistance, resilience, and the ability to hold up against heavy tons and repeated stress. The gear module, which figures out tooth size and toughness, varies in between 10 to 30, depending on mill size and application requirements. Usual pressure angles are 20 degrees, maximized for smooth fitting together with the girth gear. Pinion gears are made with strict adherence to AGMA (American Equipment Manufacturers Organization) or ISO (International Organization for Standardization) requirements, guaranteeing accuracy in tooth account, pitch, and positioning. Trick measurements, such as face width (200– 500 mm) and pitch diameter (500– 2000 mm), are personalized to match particular sphere mill arrangements. The equipment teeth are ground or hobbed to achieve a surface finish of Ra ≤ 1.6 μm, reducing rubbing and vibration throughout operation. Dynamic lots capability is calculated to handle high torque degrees, commonly exceeding 50,000 Nm, with a service element of 1.5– 2.0 for safety. Lubrication grooves or networks might be integrated to ensure regular oil circulation, lowering heat accumulation. Pinion equipments work with numerous drive systems, consisting of transmissions or direct motor links, and are often paired with alloy steel girth equipments for optimum performance. Quality control includes non-destructive testing (NDT), dimensional assessments, and dry run to validate sound degrees (85 dB) and operational effectiveness. Applications cover cement plants, extracting operations, and chemical processing, where trusted grinding is important. Upkeep entails routine placement checks, lubrication tracking, and regular wear examinations to prolong life span. Customization options consist of unique coatings (e.g., anti-corrosion), tooth profiling, or material upgrades for extreme settings. The pinion equipment is engineered for smooth integration, making certain marginal downtime and optimum performance in commercial grinding systems.
(Ball mill Pinion Gear for Ball Mill)
Applications of Ball mill Pinion Gear for Ball Mill
Ball mill pinion equipments are crucial components in the procedure of ball mills, which are widely made use of in grinding and blending materials across different sectors. These equipments form component of the drive system, transferring rotational power from the electric motor to the mill cyndrical tube, enabling the grinding process. Their layout, sturdiness, and precision straight impact the performance and long life of sphere mills. Below are essential applications of sphere mill pinion gears:
** 1. Mining and Mineral Processing: **.
Round mills are crucial in grinding ores and minerals to remove metals like gold, copper, and iron. Pinion gears sustain hefty tons and abrasive environments, ensuring regular turning for grating raw materials into great powders. Their robust building reduces wear, even when refining tough minerals.
** 2. Concrete Manufacturing: **.
In cement plants, round mills grind clinker, gypsum, and various other additives to produce cement. Pinion equipments must stand up to high torque and thermal stress and anxiety throughout prolonged operation. Precision alignment with the girth gear makes certain smooth turning, reducing power consumption and boosting grinding effectiveness.
** 3. Chemical Manufacturing: **.
Round mills mix and grind chemicals to develop uniform compounds. Pinion gears in this sector are developed to resist rust from hostile chemical settings, making certain reputable efficiency and stopping contamination during production.
** 4. Pharmaceuticals: **.
Drug ball mills refine active components and excipients into ultra-fine powders. Pinion gears here need high accuracy to keep uniform particle size circulation. Stainless steel or layered variants are typically utilized to meet hygiene and regulatory standards.
** 5. Power Generation: **.
Coal-fired nuclear power plant make use of ball mills to pulverize coal for burning. Pinion gears have to take care of rough coal dust and high rotational speeds, guaranteeing consistent gas preparation for effective power generation.
** 6. Ceramics and Paints: **.
In porcelains and repaint manufacturing, round mills grind pigments and resources to achieve desired textures and shades. Pinion gears add to regular grinding, enabling the manufacturing of high-quality, consistent items.
** Secret Functions of Quality Pinion Gears: **.
– ** Material: ** Top-quality alloy steel or specialized coverings for wear and rust resistance.
– ** Accuracy Machining: ** Ensures smooth harmonizing with the girth equipment, lowering resonance and noise.
– ** Warm Treatment: ** Procedures like carburizing boost surface area firmness and exhaustion resistance.
– ** Personalization: ** Tailored measurements and tooth profiles to suit specific mill designs.
Regular maintenance, consisting of lubrication and alignment checks, is crucial to avoid early failure. By picking long lasting, well-engineered pinion gears, industries enhance ball mill performance, minimize downtime, and lower operational expenses over the devices’s lifecycle.
Company Introduction
Established in 2007, Excavator Attachments Heavy Machinery Co.,ltd. focus on metal research and mining machinery spare parts. 2 factories over an area of 13,300 square meters, based on 100+ sets of equipment, our production capacity reaches 12000 Tons/Year. has passed ISO 9001 quality managment system certification in 2008.
Our mainly products are dragline excavator spare parts,rotary kiln spare parts, large modulus gear (gear shaft), gearbox ect. 40+ patents with over 45 years experience to help focus on improve the service life of spare parts. We belive that more than 80% reason of mechanical parts’ working life depends on hot processing (steel making/forging/casting/welding/heat treatment). Eight material engineers will control the quality from the original resource.
If you are interested, please feel free to contact us.
Payment
L/C, T/T, Western Union, Paypal, Credit Card etc.
Shipment
By sea, by air, by express, as customers request.
5 FAQs of Ball mill Pinion Gear for Ball Mill
What causes ball mill pinion gear failure? Pinion gear failure is commonly caused by misalignment, inadequate lubrication, excessive load, or wear over time. Misalignment creates uneven stress on gear teeth, leading to cracks or fractures. Poor lubrication accelerates friction and heat, causing surface degradation like pitting or scuffing. Overloading the mill beyond its capacity strains the pinion, while general wear from prolonged use erodes tooth profiles, reducing meshing efficiency. Regular inspections and addressing these issues promptly can extend gear life.
How do I maintain a ball mill pinion gear? Maintenance includes ensuring proper lubrication with high-quality grease or oil to minimize friction and heat. Regularly check gear alignment using laser tools or dial indicators to prevent uneven wear. Inspect teeth for cracks, chipping, or pitting, and clean debris to avoid contamination. Monitor operating conditions to prevent overloading, and tighten mounting bolts to specified torque levels. Scheduled downtime for thorough inspections is critical for longevity.
What material is used for ball mill pinion gears? Pinion gears are typically made from high-strength alloy steels like 4340 or 4140, which offer excellent toughness and fatigue resistance. These materials undergo heat treatment processes such as carburizing or induction hardening to enhance surface hardness (up to 55-60 HRC) while maintaining a ductile core. This combination ensures durability under heavy loads and reduces wear rates in abrasive milling environments.
Why is pinion gear alignment important? Proper alignment ensures even load distribution across gear teeth, preventing localized stress and premature failure. Misalignment causes vibration, noise, and uneven tooth contact, leading to accelerated wear, pitting, or tooth breakage. Correct alignment also improves energy efficiency and reduces strain on the drive motor. Align gears during installation and periodically using precision tools to maintain optimal performance.
How do I know if my pinion gear needs replacement? Signs include abnormal noises (grinding or knocking), excessive vibration, visible tooth damage (cracks, spalling, or missing sections), or irregular mill operation. Increased power consumption or overheating in the drive system may also indicate gear wear. Measure tooth thickness periodically; if wear exceeds 5-7% of the original profile, replacement is recommended. Proactive replacement avoids unplanned downtime and costly damage to the ball mill drive train.
(Ball mill Pinion Gear for Ball Mill)
REQUEST A QUOTE
RELATED PRODUCTS
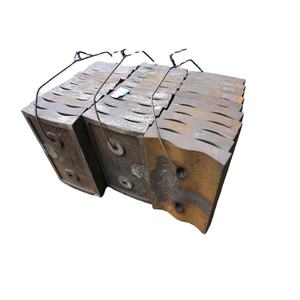
High-Quality High Manganese Steel Ball Mill Liners Reliable Wear Spare Parts for Ball Mills
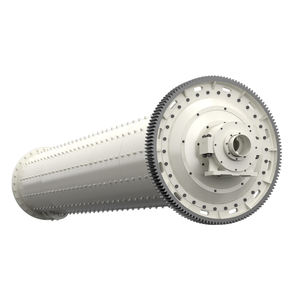
High Manganese Steel Alloy Chromium Wear Resistance Vertical Ball Mill Rubber Liner Plate Impact Crusher Wear Parts Liner
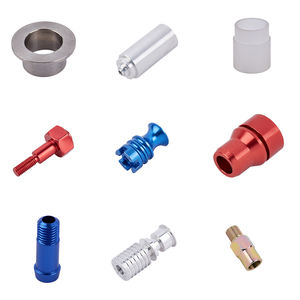
Supply Ball Mill Stone Grinding Mill Ball Mill Grinding Machine For Rock Gold Engineering and building materials machinery
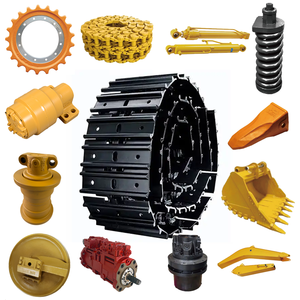
Large big 100 kg 900×3000 portable diesel engine ball mill parts for gold mining
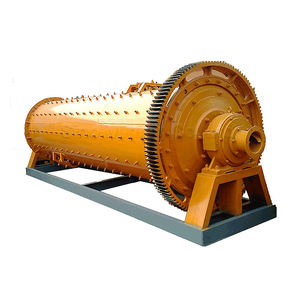
Ball mill spare parts ZQCr10 high chrome casting alloy grinding ball
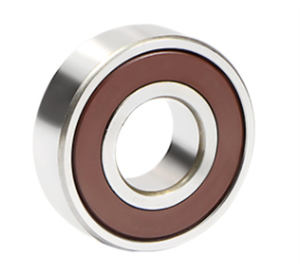