PRODUCT PARAMETERS
Description
Brief introduction of Customized Large Ball Mill Liner New Casting Parts for Ore Mining Mining Machinery Processing
Ball mill is a kind of equipment used to crush or grind materials to very fine powder, which is widely used in mining, cement, chemical industry, etc. Customized Large Ball Mill Liner New Casting Parts for Ore Mining Mining Machinery Processing refers to all kinds of parts and components which are necessary to ensure the normal operation of the ball mill, including liner plate, grinding balls, gears, bearings and so on.
Features and advantages of Customized Large Ball Mill Liner New Casting Parts for Ore Mining Mining Machinery Processing
Strong durability: Made of high-quality materials and under strict quality control, it ensures high wear resistance and long service life of spare parts.
Good interchangeability: The standardized design makes the spare parts interchangeable between different types of ball mills, simplifying the maintenance process.
Optimized design: Customised design according to the actual working conditions, which improves the working efficiency and reduces energy consumption at the same time.
Easy to install and maintain: reasonable structure, convenient for users to quickly replace and repair, reduce downtime.
Stable performance: Precision machining and rigorous testing ensure stable performance even in harsh environments.
(Customized Large Ball Mill Liner New Casting Parts for Ore Mining Mining Machinery Processing)
Specification of Customized Large Ball Mill Liner New Casting Parts for Ore Mining Mining Machinery Processing
Customized Large Sphere Mill Liners are crucial parts designed to secure the internal covering of ball mills made use of in ore mining and mineral handling operations. These liners are crafted to stand up to severe abrasion, impact, and rust triggered by grinding media and raw materials, making certain extended mill resilience and functional effectiveness.
** Product Structure: ** Produced from high-quality alloy steels, high-chromium cast iron, or manganese steel, these linings are customized to satisfy details ore solidity, mill rate, and grinding conditions. Custom-made product option makes certain ideal wear resistance, influence absorption, and longevity, even in extreme mining atmospheres.
** Requirements: ** Available in different densities (30– 150 mm), sizes (1,000– 6,000 mm), and accounts (wave, rib, step, or smooth), the liners are tailored to fit sphere mill measurements (sizes ranging from 1.5– 8 meters). Weight per liner segment differs from 100 kg to 5,000 kg, relying on mill size and application needs. Bolt-hole patterns and lining shapes are precision-engineered to make certain smooth installment and placement.
** Style Functions: ** Advanced CAD/CAM innovation is used to develop lining profiles that enhance grinding effectiveness and product flow. Specialized makes minimize power intake by minimizing slippage and improving lifting of grinding media. Changeable lifter bars and composite liners (rubber-metal crossbreeds) are readily available for applications needing noise reduction or enhanced deterioration resistance.
** Production Refine: ** Generated utilizing sand spreading, lost-wax spreading, or V-method casting, adhered to by heat treatment (quenching and tempering) to accomplish desired firmness (HRC 45– 65) and toughness. Strict quality assurance consists of ultrasonic screening, dimensional checks, and firmness confirmation to make sure defect-free performance.
** Applications: ** Perfect for refining copper, gold, iron ore, and other minerals in mining, concrete, and chemical sectors. Custom linings adapt to wet or completely dry grinding, rugged or great squashing, and high-temperature settings.
** Perks: ** Extended service life minimizes downtime and maintenance prices. Customization makes sure exact fit and compatibility with OEM mill specs. Anti-abrasion coatings or ceramic inserts can be added for extreme wear conditions.
** Assistance: ** Distributors use technological assessment to pick optimal lining products and styles based upon functional data. Post-installation support includes wear evaluation and replacement scheduling.
These linings are critical for maximizing mill performance, securing devices, and decreasing complete cost of possession in mining operations.
(Customized Large Ball Mill Liner New Casting Parts for Ore Mining Mining Machinery Processing)
Applications of Customized Large Ball Mill Liner New Casting Parts for Ore Mining Mining Machinery Processing
Personalized large ball mill liners are important elements in ore mining and mineral processing operations, made to enhance the durability and performance of grinding equipment. These liners serve as safety shields within ball mills, guarding the mill’s interior from the extreme abrasion and influence caused by grinding tough ores such as iron, copper, gold, and other minerals. Their tailored layout makes sure optimal compatibility with details mill dimensions and functional needs, making them essential in diverse mining atmospheres. One vital application is in mineral processing plants, where these liners promote the reliable grinding of raw ore right into great fragments, an important action in drawing out beneficial metals. Their personalization allows for exact positioning with mill specs, making sure smooth procedure and decreasing power waste. Making use of advanced materials like high-chromium steel, manganese alloy, or composite rubber improves wear resistance, considerably extending the lining’s life span also under extreme conditions. This decreases the regularity of replacements and maintenance downtime, translating to reduced functional prices and greater efficiency. In cement manufacturing and non-metallic mining, these liners also play an important role by taking care of abrasive materials like limestone and clinker, keeping consistent grinding performance. Customized styles address distinct difficulties, such as differing ore solidity or mill rotational speeds, by optimizing lining profiles for boosted product circulation and decreased energy intake. In addition, their durable building and construction minimizes material contamination during grinding, making certain greater purity in refined ores. By integrating advanced spreading methods such as sand casting or lost-foam techniques, makers accomplish exact geometries and enhanced mechanical buildings. The ecological benefit of these liners depends on their longevity, which decreases waste generation from frequent part replacements. In general, personalized huge sphere mill liners are essential in enhancing the integrity, effectiveness, and cost-effectiveness of mining and handling operations, making them a strategic financial investment for sectors concentrated on sustainable resource removal.
Company Introduction
Established in 2007, Excavator Attachments Heavy Machinery Co.,ltd. focus on metal research and mining machinery spare parts. 2 factories over an area of 13,300 square meters, based on 100+ sets of equipment, our production capacity reaches 12000 Tons/Year. has passed ISO 9001 quality managment system certification in 2008.
Our mainly products are dragline excavator spare parts,rotary kiln spare parts, large modulus gear (gear shaft), gearbox ect. 40+ patents with over 45 years experience to help focus on improve the service life of spare parts. We belive that more than 80% reason of mechanical parts’ working life depends on hot processing (steel making/forging/casting/welding/heat treatment). Eight material engineers will control the quality from the original resource.
If you are interested, please feel free to contact us.
Payment
L/C, T/T, Western Union, Paypal, Credit Card etc.
Shipment
By sea, by air, by express, as customers request.
5 FAQs of Customized Large Ball Mill Liner New Casting Parts for Ore Mining Mining Machinery Processing
**1. What materials are used in your customized large ball mill liners, and why are they suitable for ore mining?** Our ball mill liners are crafted from high-grade alloys like chromium-molybdenum steel, high-manganese steel, or specially formulated wear-resistant ceramics. These materials are chosen for their exceptional hardness, impact resistance, and ability to withstand abrasion from grinding ores. They minimize wear, extend liner lifespan, and maintain grinding efficiency in harsh mining environments.
**2. How does customization improve the performance of ball mill liners?** Customization ensures liners are tailored to your mill’s dimensions, ore type, and operational conditions (e.g., wet or dry grinding). Optimized design factors like lifter height, groove patterns, and thickness distribution enhance grinding media motion, reduce energy consumption, and improve ore breakdown efficiency. This results in higher throughput, reduced downtime, and lower long-term costs.
**3. What is the typical lifespan of these liners, and how can it be extended?** Lifespan varies based on material, ore abrasiveness, and operating hours, but our liners typically last 6–24 months. Regular maintenance, such as monitoring wear patterns, avoiding overloading, and ensuring proper alignment during installation, can prolong service life. Using liners with reinforced impact zones or replaceable segments further optimizes longevity.
**4. How do you ensure precise fitting for customized liners?** We use advanced 3D scanning and CAD modeling to capture exact mill dimensions, including shell curvature and bolt-hole patterns. This data guides precision casting and machining, ensuring seamless fitment. Post-production inspections verify dimensional accuracy, eliminating gaps or misalignment that cause premature wear or mill vibration.
**5. Are these liners compatible with different types of ore processing?** Yes. Our liners are designed to handle diverse ores, from soft minerals like limestone to hard, abrasive ores like iron or copper. Material selection and design adjustments (e.g., thicker profiles for high-impact ores, smoother surfaces for fine grinding) ensure optimal performance across applications. We also offer corrosion-resistant coatings for wet grinding or acidic environments.
(Customized Large Ball Mill Liner New Casting Parts for Ore Mining Mining Machinery Processing)
REQUEST A QUOTE
RELATED PRODUCTS
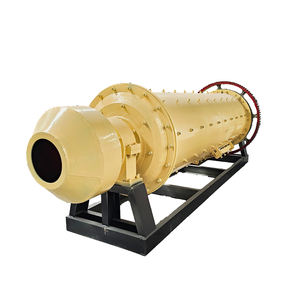
Low Cost Factory Directly Spare Parts of Grinding Ball Mill Provided AC Motor Viet Nam Ball Milling Machine Energy & Mining
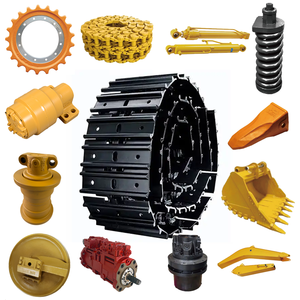
Large big 100 kg 900×3000 portable diesel engine ball mill parts for gold mining
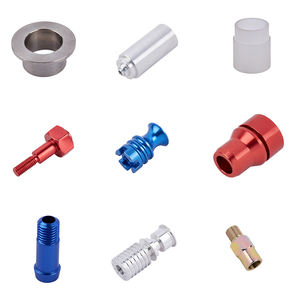
Bode Pneumatic Clutch Ball Mill Side plate for Mining Machinery
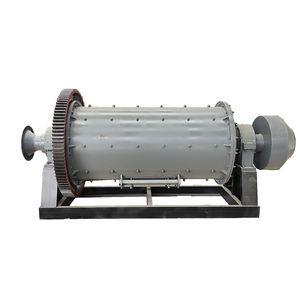
Hot Mining Machinery Parts High Manganese Steel Balls Forged Grinding Ball Media for Ball Mill
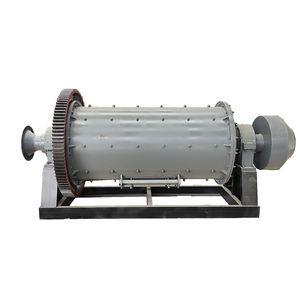
OEM customize cast alloy ball mill liners wear resistant lining plate spare parts
