PRODUCT PARAMETERS
Description
Brief introduction of Gold Ore Lead Zinc Copper Mining Stone Mini Steel Coal Steel Used Wet Ball Mill and Dry Ball Mill for Mining Grinding
Ball mill is a kind of equipment used to crush or grind materials to very fine powder, which is widely used in mining, cement, chemical industry, etc. Gold Ore Lead Zinc Copper Mining Stone Mini Steel Coal Steel Used Wet Ball Mill and Dry Ball Mill for Mining Grinding refers to all kinds of parts and components which are necessary to ensure the normal operation of the ball mill, including liner plate, grinding balls, gears, bearings and so on.
Features and advantages of Gold Ore Lead Zinc Copper Mining Stone Mini Steel Coal Steel Used Wet Ball Mill and Dry Ball Mill for Mining Grinding
Strong durability: Made of high-quality materials and under strict quality control, it ensures high wear resistance and long service life of spare parts.
Good interchangeability: The standardized design makes the spare parts interchangeable between different types of ball mills, simplifying the maintenance process.
Optimized design: Customised design according to the actual working conditions, which improves the working efficiency and reduces energy consumption at the same time.
Easy to install and maintain: reasonable structure, convenient for users to quickly replace and repair, reduce downtime.
Stable performance: Precision machining and rigorous testing ensure stable performance even in harsh environments.
(Gold Ore Lead Zinc Copper Mining Stone Mini Steel Coal Steel Used Wet Ball Mill and Dry Ball Mill for Mining Grinding)
Specification of Gold Ore Lead Zinc Copper Mining Stone Mini Steel Coal Steel Used Wet Ball Mill and Dry Ball Mill for Mining Grinding
The ball mill is a critical equipment in mining operations, designed for grinding various ores and materials such as gold, lead-zinc, copper, coal, steel slag, and stone. It is available in both wet and dry configurations, catering to different processing requirements. Wet ball mills utilize water to form a slurry, ideal for finer grinding and materials requiring moisture, while dry ball mills operate without water, suitable for moisture-sensitive substances or where dry processing is preferred. These mills are widely used in mining, metallurgy, cement, and construction industries for efficient material size reduction. Key specifications include model variations like MQG (wet) and MQY (dry), with cylinder diameters ranging from 900 mm to 5500 mm and lengths from 1800 mm to 8500 mm. Capacities span from 0.5 t/h for smaller units to over 200 t/h for industrial-scale models. Motor power ranges between 5.5 kW and 630 kW, driving rotation speeds of 20–30 rpm. The grinding chamber is lined with wear-resistant materials and filled with steel balls (15–150 mm diameter) as grinding media, ensuring durability and efficient pulverization. Processed materials include gold ore, lead-zinc, copper, coal, limestone, quartz, granite, steel slag, and recycled metals. Features include robust welded steel construction, corrosion-resistant coatings, adjustable discharge fineness, overload protection, and low-noise operation. Wet mills excel in producing ultra-fine particles with higher efficiency, while dry mills prevent material contamination. Customization options allow for tailored solutions in drum dimensions, motor power, and material compatibility. Designed for reliability, these mills offer easy maintenance with accessible inspection hatches and lubrication systems. Their versatility in handling diverse minerals and operational conditions makes them indispensable in mineral processing, cement production, and industrial grinding applications, ensuring optimal performance across small-scale and large mining projects.
(Gold Ore Lead Zinc Copper Mining Stone Mini Steel Coal Steel Used Wet Ball Mill and Dry Ball Mill for Mining Grinding)
Applications of Gold Ore Lead Zinc Copper Mining Stone Mini Steel Coal Steel Used Wet Ball Mill and Dry Ball Mill for Mining Grinding
Ball mills are essential equipment in the mining and mineral processing industries, designed to grind materials into fine powders for efficient extraction of valuable metals. The wet ball mill and dry ball mill are two primary variants used across applications involving gold ore, lead, zinc, copper, coal, steel, and stone. Each type offers distinct advantages depending on material properties, moisture content, and operational requirements.
Wet Ball Mill Applications:
Wet grinding is ideal for materials requiring slurry formation or moisture-sensitive processes. In gold ore processing, wet ball mills pulverize ore into a slurry, enhancing gold recovery through cyanidation or flotation. For lead-zinc and copper ores, wet grinding ensures efficient liberation of minerals from gangue, critical for froth flotation separation. Coal processing may use wet mills to grind coal-water mixtures for specific industrial uses. The wet method minimizes dust, reduces heat generation, and ensures finer particle size distribution, making it suitable for abrasive or sticky materials like limestone or clay in cement production.
Dry Ball Mill Applications:
Dry grinding is preferred when moisture must be avoided or materials are processed in arid environments. In steel and mini steel plants, dry ball mills grind raw materials like iron ore, coal, and limestone to produce pulverized coal for blast furnaces or cementitious additives. Copper and zinc concentrates often undergo dry milling before smelting to control moisture levels. Dry mills are also used for grinding silica, feldspar, and other non-metallic minerals in ceramics and glass manufacturing. The absence of water simplifies maintenance, reduces energy costs, and avoids slurry handling, making dry mills cost-effective for heat-resistant or non-reactive materials.
Key Considerations:
Wet ball mills excel in producing ultra-fine particles and handling high-moisture ores but require water resources and slurry management. Dry mills offer operational simplicity and lower environmental impact in water-scarce regions but may generate more dust. Both types are integral to mining circuits, with selection depending on ore type, downstream processes, and cost efficiency.
From precious metal extraction to industrial mineral processing, wet and dry ball mills enable efficient material size reduction, ensuring optimal recovery and quality in mining operations. Their versatility makes them indispensable in transforming raw ores and minerals into valuable commodities.
Company Introduction
Established in 2007, Excavator Attachments Heavy Machinery Co.,ltd. focus on metal research and mining machinery spare parts. 2 factories over an area of 13,300 square meters, based on 100+ sets of equipment, our production capacity reaches 12000 Tons/Year. has passed ISO 9001 quality managment system certification in 2008.
Our mainly products are dragline excavator spare parts,rotary kiln spare parts, large modulus gear (gear shaft), gearbox ect. 40+ patents with over 45 years experience to help focus on improve the service life of spare parts. We belive that more than 80% reason of mechanical parts’ working life depends on hot processing (steel making/forging/casting/welding/heat treatment). Eight material engineers will control the quality from the original resource.
If you are interested, please feel free to contact us.
Payment
L/C, T/T, Western Union, Paypal, Credit Card etc.
Shipment
By sea, by air, by express, as customers request.
5 FAQs of Gold Ore Lead Zinc Copper Mining Stone Mini Steel Coal Steel Used Wet Ball Mill and Dry Ball Mill for Mining Grinding
What is the difference between a wet ball mill and a dry ball mill? Wet ball mills use water or another liquid as a grinding medium, which helps reduce dust, lower temperatures, and improve material flow for finer grinding. Dry ball mills operate without liquid, relying on airflow, making them suitable for moisture-sensitive materials or when a dry final product is required. Wet mills are ideal for ores like gold, copper, lead, or zinc, while dry mills are better for coal, limestone, or cement.
What are the advantages of using a wet ball mill in mining? Wet ball mills excel in grinding efficiency for high-moisture or slurry-based ores, producing a finer, more uniform particle size. They minimize heat generation, reducing the risk of material combustion, and are better for processing abrasive ores like gold or copper. Water also suppresses dust, improving workplace safety. However, they require more maintenance due to corrosion and slurry handling.
When should I choose a dry ball mill over a wet ball mill? Opt for a dry ball mill if your material is sensitive to moisture (e.g., coal, gypsum) or if the final product must be dry. Dry mills are simpler to operate, with lower installation and maintenance costs, and are ideal for arid regions with water scarcity. They’re less effective for ultrafine grinding but work well for harder ores like steel slag or limestone.
Which materials are suitable for wet and dry ball mills? Wet ball mills handle gold, copper, lead-zinc, and nickel ores, as well as non-metallic minerals requiring slurry processing. Dry ball mills process coal, cement clinker, limestone, iron ore, and steel slag. Mini steel plants often use dry mills for grinding coal or additives, while mining operations for precious metals prefer wet milling for higher recovery rates.
How does maintenance differ between wet and dry ball mills? Wet mills require frequent checks for corrosion, slurry leakage, and liner wear due to water exposure. Seals and pumps need regular upkeep. Dry mills face challenges with dust control and abrasion but avoid water-related corrosion. Both types need routine lubrication, gear inspections, and grinding media replacement. Dry mills generally have lower long-term maintenance costs but may require dust filtration systems.
What factors affect the capacity and efficiency of these ball mills? Key factors include ore hardness, feed size, grinding media type, rotation speed, and discharge method. Wet mills achieve higher efficiency with viscous slurries, while dry mills depend on airflow and material dryness. Adjusting water content (wet) or ventilation (dry) optimizes output. For mini steel or coal grinding, dry mills prioritize speed; for metal ores, wet mills focus on particle fineness.
(Gold Ore Lead Zinc Copper Mining Stone Mini Steel Coal Steel Used Wet Ball Mill and Dry Ball Mill for Mining Grinding)
REQUEST A QUOTE
RELATED PRODUCTS
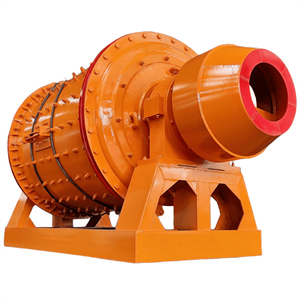
heavy duty mining ball mill spare part 42CrMo steel hollow shaft
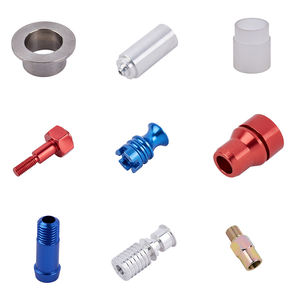
High Manganese Steel Casting Ball Mill Wear Spare Parts Ball Mill Liners
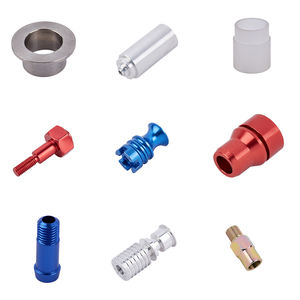
Supply Ball Mill Stone Grinding Mill Ball Mill Grinding Machine For Rock Gold Engineering and building materials machinery
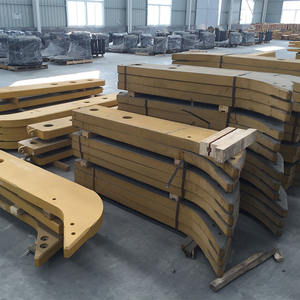
Industrial Ball Milling Gold Ore Ball Mill For Mineral Ball Mill For Stone Gold
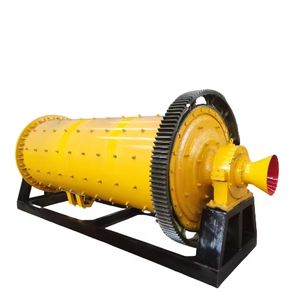
Most Searched for Tool 2023 OEM Low Good Quality Custom Liners Ball Mill Parts Cement Making Wear Resistant High Chrome
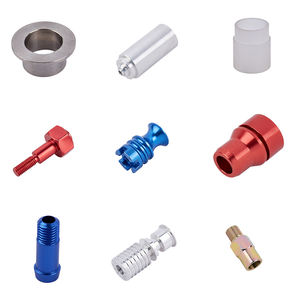