PRODUCT PARAMETERS
Description
Brief introduction of heavy duty Casting Steel ball mill spur wheel gear
Ball mill is a kind of equipment used to crush or grind materials to very fine powder, which is widely used in mining, cement, chemical industry, etc. heavy duty Casting Steel ball mill spur wheel gear refers to all kinds of parts and components which are necessary to ensure the normal operation of the ball mill, including liner plate, grinding balls, gears, bearings and so on.
Features and advantages of heavy duty Casting Steel ball mill spur wheel gear
Strong durability: Made of high-quality materials and under strict quality control, it ensures high wear resistance and long service life of spare parts.
Good interchangeability: The standardized design makes the spare parts interchangeable between different types of ball mills, simplifying the maintenance process.
Optimized design: Customised design according to the actual working conditions, which improves the working efficiency and reduces energy consumption at the same time.
Easy to install and maintain: reasonable structure, convenient for users to quickly replace and repair, reduce downtime.
Stable performance: Precision machining and rigorous testing ensure stable performance even in harsh environments.
(heavy duty Casting Steel ball mill spur wheel gear)
Specification of heavy duty Casting Steel ball mill spur wheel gear
Heavy-duty casting steel ball mill spur wheel gears handle high-stress industrial grinding operations. Made from high-quality alloy steel, these gears ensure durability under extreme loads. Common materials include ASTM A148 or equivalent grades, chosen for strength and wear resistance. The steel composition balances carbon, manganese, chromium, and molybdenum to optimize hardness and toughness. Heat treatment processes like quenching and tempering enhance surface hardness while maintaining core flexibility. Surface hardness typically reaches 50-55 HRC, reducing wear from friction. Inner layers stay tough to absorb impact forces. Precision machining ensures accurate tooth profiles for smooth engagement with pinion gears. Gear teeth undergo grinding or hobbing to achieve tight tolerances. Backlash control minimizes vibration during operation. Flange-mounted designs allow easy installation on ball mill shells. Bolt holes align with standard mill configurations for compatibility. Large diameters range from 1 meter to over 5 meters, matching industrial mill sizes. Custom dimensions accommodate specific machinery requirements. Load capacities support thousands of kilowatts of transmitted power. High torque resistance prevents deformation under heavy loads. Gear teeth feature reinforced roots to avoid cracking. Advanced lubrication channels reduce heat buildup. Oil grooves distribute lubricant evenly across gear surfaces. Anti-corrosion coatings protect against moisture and chemicals. Zinc plating or epoxy layers extend service life in harsh environments. Noise reduction designs lower operational sound levels. Precision alignment cuts down on gear chatter. Dynamic balancing minimizes rotational imbalances. Testing includes ultrasonic checks for internal flaws. Magnetic particle inspection detects surface cracks. Each gear meets ISO 9001 quality standards. Performance certifications ensure reliability. Applications cover mining, cement production, and mineral processing. These gears suit raw mills, coal mills, and clinker mills. Custom gear ratios optimize speed and torque for different processes. Replaceable segments simplify maintenance. Modular designs reduce downtime during repairs. Technical support covers installation guidance and troubleshooting. Spare parts availability ensures long-term operation.
(heavy duty Casting Steel ball mill spur wheel gear)
Applications of heavy duty Casting Steel ball mill spur wheel gear
Heavy-duty casting steel ball mill spur wheel gears are essential in industries requiring heavy material processing. These gears transfer power in ball mills. They grind raw materials into fine powders. Mining operations use them extensively. Cement production plants rely on them for grinding clinker. Chemical processing industries employ these gears to crush hard substances. Their design handles high torque and heavy loads. This ensures smooth operation under extreme conditions.
The gears are made from high-grade steel alloys. Advanced casting methods improve their strength. Heat treatment processes enhance wear resistance. This extends their service life. Their teeth are precision-machined. This reduces friction during rotation. Proper alignment minimizes energy loss. Operators see lower maintenance costs over time.
Durability is a key advantage. These gears withstand abrasive materials. They resist impact from heavy loads. Harsh environments like high temperatures do not degrade them. This reliability reduces downtime in production lines. Factories achieve consistent output. Processing efficiency improves significantly.
Customization options meet specific needs. Gear sizes vary based on mill dimensions. Tooth profiles adapt to different speed requirements. Surface coatings are available for extra corrosion protection. Engineers work closely with clients. They ensure each gear matches operational demands.
Regular maintenance is simple. Inspections check for wear patterns. Lubrication systems keep gears running smoothly. Damaged teeth can be repaired or replaced. This prevents complete gear failure. Operators save money on replacements.
Heavy-duty casting steel ball mill spur wheel gears are critical in heavy industries. Their robust construction ensures long-term performance. They handle the toughest grinding tasks. Companies trust them for reliable power transmission. Productivity stays high. Operational costs remain manageable.
Company Introduction
Established in 2007, Excavator Attachments Heavy Machinery Co.,ltd. focus on metal research and mining machinery spare parts. 2 factories over an area of 13,300 square meters, based on 100+ sets of equipment, our production capacity reaches 12000 Tons/Year. has passed ISO 9001 quality managment system certification in 2008.
Our mainly products are dragline excavator spare parts,rotary kiln spare parts, large modulus gear (gear shaft), gearbox ect. 40+ patents with over 45 years experience to help focus on improve the service life of spare parts. We belive that more than 80% reason of mechanical parts’ working life depends on hot processing (steel making/forging/casting/welding/heat treatment). Eight material engineers will control the quality from the original resource.
If you are interested, please feel free to contact us.
Payment
L/C, T/T, Western Union, Paypal, Credit Card etc.
Shipment
By sea, by air, by express, as customers request.
5 FAQs of heavy duty Casting Steel ball mill spur wheel gear
What materials are used in heavy-duty casting steel ball mill spur wheel gears? High-grade alloy steel is the main material. Carbon, chromium, manganese are added for strength. Heat treatment processes like quenching and tempering improve hardness. This ensures the gear handles heavy loads without wearing down quickly.
How is the spur wheel gear manufactured? The gear starts as molten steel poured into precision molds. Casting methods like sand casting or lost-wax casting create the initial shape. Machining refines gear teeth for accurate meshing. Quality checks confirm dimensions and surface finish meet standards.
What makes this gear suitable for heavy-duty ball mills? The design focuses on high torque and shock resistance. Thick gear teeth distribute stress evenly. Durable materials prevent cracks under continuous operation. These features reduce downtime in mining or cement industries.
How do I maintain the spur wheel gear? Inspect gear teeth regularly for wear or damage. Clean debris from the gear surface after shifts. Apply high-viscosity lubricant to minimize friction. Replace the gear if cracks or severe pitting appear. Proper maintenance extends service life.
Can the gear be customized for specific machinery? Yes. Manufacturers adjust gear diameter, module, and teeth count. Custom bore sizes fit different shafts. Special coatings or hardening techniques address unique operational needs. Provide machine specs to get the right gear.
(heavy duty Casting Steel ball mill spur wheel gear)
REQUEST A QUOTE
RELATED PRODUCTS
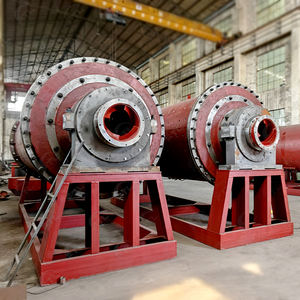
Mining energy ball mill metal matric ceramic parts ceramic table liner grinding roller
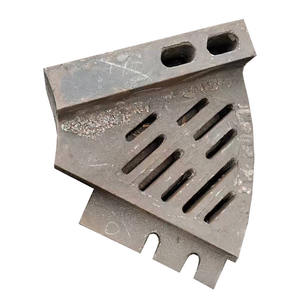
Low worth buying products Mining Grinding Mill Trommel Scrubber Wear Parts Rubber Ball Mill Liner For
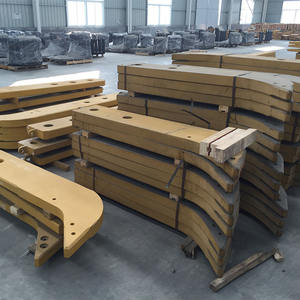
10 Tph Ball Mill ,Overflow Ball Grinder Mill Mining Machine,Ball Mill 900*1800
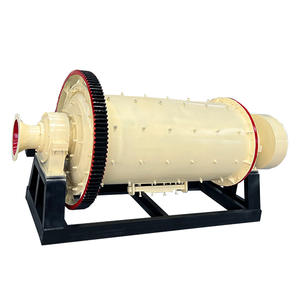
Gear Shaft For Ball Mill Spline Gear Shaft Mining Spare Parts Gear Shaft For Gearbox
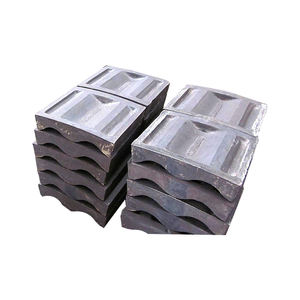
ball mill parts liner plates sag mill liners / ball mill rubber liner
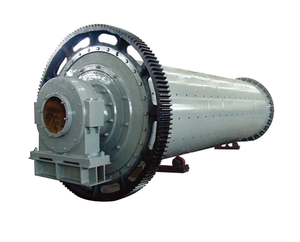