PRODUCT PARAMETERS
Description
Brief introduction of Industrial ball mill grinding machinery equipment wet and dry cement dressing crushing
Ball mill is a kind of equipment used to crush or grind materials to very fine powder, which is widely used in mining, cement, chemical industry, etc. Industrial ball mill grinding machinery equipment wet and dry cement dressing crushing refers to all kinds of parts and components which are necessary to ensure the normal operation of the ball mill, including liner plate, grinding balls, gears, bearings and so on.
Features and advantages of Industrial ball mill grinding machinery equipment wet and dry cement dressing crushing
Strong durability: Made of high-quality materials and under strict quality control, it ensures high wear resistance and long service life of spare parts.
Good interchangeability: The standardized design makes the spare parts interchangeable between different types of ball mills, simplifying the maintenance process.
Optimized design: Customised design according to the actual working conditions, which improves the working efficiency and reduces energy consumption at the same time.
Easy to install and maintain: reasonable structure, convenient for users to quickly replace and repair, reduce downtime.
Stable performance: Precision machining and rigorous testing ensure stable performance even in harsh environments.
(Industrial ball mill grinding machinery equipment wet and dry cement dressing crushing)
Specification of Industrial ball mill grinding machinery equipment wet and dry cement dressing crushing
Industrial ball mill grinding machinery equipment handles damp and completely dry concrete dressing and crushing jobs. This equipment grinds resources into great powders for concrete production. It works in mining, construction, and chemical markets. The tools refines materials like cement clinker, silicate items, fertilizers, and non-ferrous metals.
The maker makes use of steel or ceramic grinding rounds. These balls squash materials with rotation inside a round chamber. The chamber’s lining stands up to wear. It decreases maintenance demands. Electric motor power ranges from 18.5 kW to 4500 kW. Ability varies from 0.65 lots per hour to 300 bunches per hour. Chamber sizes extend from 0.9 meters to 4.5 meters. Lengths cover 1.8 meters to 8 meters. Turning speed remains between 12 RPM and 40 RPM.
The devices sustains both damp and dry grinding. Wet grinding mixes materials with water. It creates slurry for much easier mixing. Dry grinding processes products without fluids. It suits moisture-sensitive applications. The maker readjusts discharge fineness. It makes use of grate plates or overflow techniques. Fragment size control makes certain uniformity.
Robust building and construction assures lasting use. Sturdy steel frameworks soak up resonance. Gearboxes transfer power smoothly. Bearings decrease friction. Electric electric motors meet power effectiveness criteria. Air conditioning systems protect against getting too hot. Safety functions consist of emergency quits and overload security.
Operators gain access to the maker conveniently. Control panels simplify rate and timing changes. Lubrication points are clearly noted. Maintenance checks call for standard devices. Extra parts like liners and grinding spheres are widely offered.
The equipment incorporates with cement production lines. It attaches to crushers, kilns, and separators. Automation choices allow remote monitoring. Sensing units track temperature level, stress, and output high quality. Custom arrangements fit specific plant designs.
This equipment enhances product reactivity. Consistent bit size increases concrete toughness. Minimized power use decreases functional prices. Minimal downtime boosts productivity. It fulfills worldwide standards for commercial grinding. Safety certifications ensure conformity with office laws.
The layout concentrates on customer convenience. Gain access to hatches streamline internal assessments. Quick-release mechanisms rate component substitutes. Sound reduction features develop safer atmospheres. Dust collection systems keep air quality.
Dependability makes this machinery a core part in cement plants. It adapts to differing product hardness and wetness degrees. Constant performance supports massive production demands.
(Industrial ball mill grinding machinery equipment wet and dry cement dressing crushing)
Applications of Industrial ball mill grinding machinery equipment wet and dry cement dressing crushing
Industrial ball mill grinding machinery is essential devices in concrete production. It takes care of basic material handling and clinker grinding. The equipment helps both damp and completely dry approaches. Dry grinding prevails in concrete plants. It turns raw materials like limestone, clay, and iron ore right into great powder. This powder mixes equally prior to getting in the kiln. Wet grinding uses water to develop a slurry. This technique fits sticky materials or when fluid additives are needed. The slurry streams smoothly for further mixing.
Sphere mills crush and grind products inside a rotating drum. Steel rounds inside struck the products to break them down. The drum’s rate regulates the grinding performance. Faster turning raises the balls greater for stronger impact. Slower turning allows them roll for finer grinding. Readjusting ball dimension and product improves results. Bigger spheres crush larger bits. Smaller sized ones improve the powder.
In concrete dressing, round mills prepare raw mix for kiln heating. The ground powder responds better during burning. Consistent bit dimension makes sure even home heating. This lowers power waste and increases clinker high quality. After melting, round mills grind clinker right into concrete powder. Plaster or other ingredients mix in during this step. The end product meets stamina and setup time requirements.
Crushing hard products is another use. Round mills handle ores, minerals, and industrial waste. They transform big portions right into workable sizes. This prepares materials for further processing. Damp grinding prevents dust and cools down heat-sensitive materials. Dry grinding conserves water and matches arid regions. Both techniques adjust to different sector needs.
The machinery operates in mining, chemicals, and ceramics. It grinds coal for power plants. It refines pigments for paints. It refines metal powders for production. Ball mills are sturdy and low-maintenance. Straightforward design cuts downtime. Normal checks on linings and bearings maintain them running. Energy-efficient models reduced operating costs.
Industrial ball mills are flexible. They adapt to product solidity and outcome demands. Automation manages speed and feeding. Sensors monitor temperature and stress. Operators modify settings for ideal efficiency. Safety and security functions secure versus overloads and leaks. Correct usage prolongs service life. Educating makes certain smooth procedure.
Company Introduction
Established in 2007, Excavator Attachments Heavy Machinery Co.,ltd. focus on metal research and mining machinery spare parts. 2 factories over an area of 13,300 square meters, based on 100+ sets of equipment, our production capacity reaches 12000 Tons/Year. has passed ISO 9001 quality managment system certification in 2008.
Our mainly products are dragline excavator spare parts,rotary kiln spare parts, large modulus gear (gear shaft), gearbox ect. 40+ patents with over 45 years experience to help focus on improve the service life of spare parts. We belive that more than 80% reason of mechanical parts’ working life depends on hot processing (steel making/forging/casting/welding/heat treatment). Eight material engineers will control the quality from the original resource.
If you are interested, please feel free to contact us.
Payment
L/C, T/T, Western Union, Paypal, Credit Card etc.
Shipment
By sea, by air, by express, as customers request.
5 FAQs of Industrial ball mill grinding machinery equipment wet and dry cement dressing crushing
What is the main difference between wet and dry grinding in industrial ball mills? Wet grinding uses water or liquid to mix with raw materials. Dry grinding processes materials without liquid. Wet methods reduce dust and handle sticky materials better. Dry methods save energy and suit heat-sensitive materials. Both methods adjust based on material properties and final product needs.
How does an industrial ball mill work for cement crushing and grinding? The machine rotates a cylinder filled with steel balls and raw materials. The rotation causes the balls to fall and hit the materials. Impact and friction break particles into smaller sizes. Cement clinker and additives are ground into fine powder. Particle size is controlled by rotation speed and grinding time.
What materials can industrial ball mills process in cement production? These mills handle cement clinker, limestone, slag, and gypsum. They grind both raw materials for cement mixing and finished cement products. Wet mills process clay or sticky substances. Dry mills crush harder, dry minerals. Material hardness, moisture, and desired fineness decide the suitable grinding method.
What factors affect grinding efficiency in industrial ball mills? Rotation speed influences how high balls lift and impact materials. Ball size and quantity determine crushing force and contact area. Material feed rate must match the mill’s capacity. Overloading slows grinding. Underloading wastes energy. Proper liner design reduces wear and maintains grinding consistency. Regular checks on these factors optimize performance.
How is maintenance managed for industrial ball mill grinding machinery? Inspect liners and balls for wear monthly. Replace damaged parts quickly to avoid uneven grinding. Lubricate bearings and gears weekly to prevent overheating. Check motor alignment and belt tension every three months. Clean the mill interior after shutdowns to remove material buildup. Record maintenance dates and observations for future reference.
(Industrial ball mill grinding machinery equipment wet and dry cement dressing crushing)
REQUEST A QUOTE
RELATED PRODUCTS
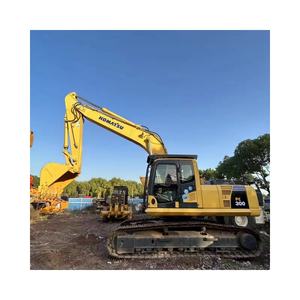
Shandong Mining Machinery Consumables MQG series rolling bearing ball mill
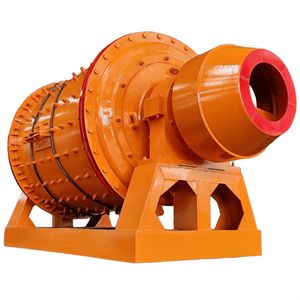
ball mill parts liner plates rubber ball mill liner /ball mill rubber liner
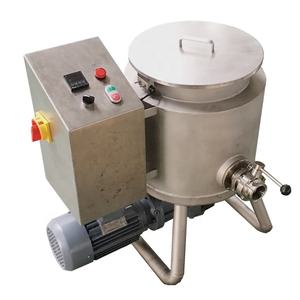
ball mill parts liner plates / complete set of feed head liner for cement mill liner plate
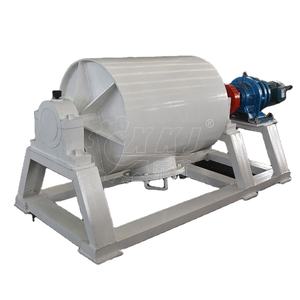
Large Capacity Ball Mill 3200X4500 for Crushing Chrome Ore, Spare Parts Supply All Provided AC Motor South Africa 85000
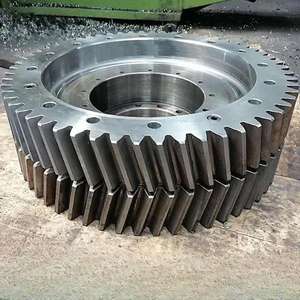
cement ball mill machine stone grinding with ball mill parts
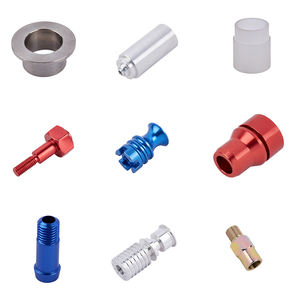