PRODUCT PARAMETERS
Description
Brief introduction of Industrial Ball Mill Mineral Grindingfor Dry Wet Production Line – MineralProcessing
Ball mill is a kind of equipment used to crush or grind materials to very fine powder, which is widely used in mining, cement, chemical industry, etc. Industrial Ball Mill Mineral Grindingfor Dry Wet Production Line – MineralProcessing refers to all kinds of parts and components which are necessary to ensure the normal operation of the ball mill, including liner plate, grinding balls, gears, bearings and so on.
Features and advantages of Industrial Ball Mill Mineral Grindingfor Dry Wet Production Line – MineralProcessing
Strong durability: Made of high-quality materials and under strict quality control, it ensures high wear resistance and long service life of spare parts.
Good interchangeability: The standardized design makes the spare parts interchangeable between different types of ball mills, simplifying the maintenance process.
Optimized design: Customised design according to the actual working conditions, which improves the working efficiency and reduces energy consumption at the same time.
Easy to install and maintain: reasonable structure, convenient for users to quickly replace and repair, reduce downtime.
Stable performance: Precision machining and rigorous testing ensure stable performance even in harsh environments.
(Industrial Ball Mill Mineral Grindingfor Dry Wet Production Line – MineralProcessing)
Specification of Industrial Ball Mill Mineral Grindingfor Dry Wet Production Line – MineralProcessing
The industrial round mill is built for grinding minerals in completely dry and wet assembly line. It takes care of products like concrete, silicates, porcelains, and ores. The maker functions by turning a steel cyndrical tube filled with grinding media, normally steel balls. This squashes and grinds basic materials right into great powders. Its design supports both dry and damp procedures. For wet grinding, water or liquid additives blend with feed product to form a slurry. This improves effectiveness and minimizes dirt.
The sphere mill’s structure consists of a hollow round shell, bearings, a drive system, and liners. The shell turns on horizontal axes. Linings safeguard the cyndrical tube from wear. Grinding media fill about 30% of the cylinder’s quantity. Material goes into through one end and departures with the other. Fragment size is controlled by adjusting grinding time, media dimension, and turning speed.
Motor power ranges from 15 kW to 4500 kW. Capability varies from 0.5 bunches per hour to over 150 lots. Dry grinding generates finer fragments. Damp grinding suits products needing slurry type. Discharge approaches include grate and overflow kinds. Grate discharge enables faster material flow. Overflow discharge guarantees better grinding.
The maker makes use of premium steel and wear-resistant alloys. This expands service life. It runs efficiently with low vibration. Upkeep is straightforward. Gain access to points allow employees check and change components conveniently. Lubrication systems reduce friction. Security functions prevent overheating and overload.
Personalization is offered. Individuals pick cylinder dimension, motor kind, lining materials, and control systems. Choices consist of automated feeders and digital tracking. The ball mill incorporates with crushers, classifiers, and conveyors. This produces full mineral processing lines.
Applications cover mining, metallurgy, cement, and chemicals. It processes quartz, feldspar, copper ore, iron ore, and more. Wet grinding benefit gold, copper, and zinc beneficiation. Dry grinding fits concrete and plant food manufacturing.
Energy performance is a key emphasis. Enhanced styles reduced power use. Sound degrees stay listed below 85 dB. The maker fulfills international criteria for safety and ecological influence. It deals with continual operation in severe conditions.
Operators adjust rate and media tons for different products. Fine powders require smaller media and longer grinding. Crude products make use of bigger media and faster turning. Control systems keep regular output quality.
Extra components include linings, bearings, gears, and motors. Providers provide technical assistance for installment and troubleshooting. Normal checks guarantee peak efficiency. Correct use lessens downtime and repair work prices.
(Industrial Ball Mill Mineral Grindingfor Dry Wet Production Line – MineralProcessing)
Applications of Industrial Ball Mill Mineral Grindingfor Dry Wet Production Line – MineralProcessing
Industrial ball mills play a vital role in mineral processing for dry and wet production lines. These equipments grind raw materials right into fine powders, enabling reliable removal of valuable minerals. They deal with different ores like quartz, feldspar, and iron ore, adapting to various hardness levels. Their design sustains both dry and damp grinding techniques, making them flexible for multiple sectors.
In dry grinding, products get in the mill without added liquid. This technique matches moisture-sensitive minerals or final products requiring completely dry powder form. The ball mill crushes products utilizing steel rounds, turning to produce friction and effect. Dry grinding is common in concrete production, developing fine clinker powder. It additionally works for porcelains, where exact particle size issues.
Wet grinding mixes products with water or solvents. This reduces dirt and improves flow for sure minerals. The slurry procedure helps different target minerals from waste, common in steel ore processing. Wet grinding creates finer bits than dry methods, suitable for chemicals or paints needing ultra-smooth textures.
Industrial round mills offer mining, building and construction, and chemical markets. In mining, they prepare ores for additional splitting up steps. Concrete plants use them to grind sedimentary rock and plaster. Ceramic factories count on sphere mills to process clay and glazes. Chemical markets grind resources for plant foods or pigments.
These mills use high effectiveness due to durable building and maximized energy usage. They handle constant operation, decreasing downtime. Steel liners and grinding rounds withstand wear, cutting upkeep prices. Advanced models include flexible rotation rates for far better control over bit size.
Personalization choices meet specific manufacturing requirements. Mills differ in size, capacity, and material compatibility. Some include cooling down systems to prevent overheating throughout grinding. Others make use of special cellular linings to stay clear of contamination in high-purity applications. Manufacturers tailor sphere mills to fit existing production lines, making sure smooth integration.
The choice between completely dry and wet grinding depends upon product buildings and end-use demands. Both approaches make certain consistent result high quality. Industrial sphere mills stay important for changing raw minerals into useful kinds across global markets.
Company Introduction
Established in 2007, Excavator Attachments Heavy Machinery Co.,ltd. focus on metal research and mining machinery spare parts. 2 factories over an area of 13,300 square meters, based on 100+ sets of equipment, our production capacity reaches 12000 Tons/Year. has passed ISO 9001 quality managment system certification in 2008.
Our mainly products are dragline excavator spare parts,rotary kiln spare parts, large modulus gear (gear shaft), gearbox ect. 40+ patents with over 45 years experience to help focus on improve the service life of spare parts. We belive that more than 80% reason of mechanical parts’ working life depends on hot processing (steel making/forging/casting/welding/heat treatment). Eight material engineers will control the quality from the original resource.
If you are interested, please feel free to contact us.
Payment
L/C, T/T, Western Union, Paypal, Credit Card etc.
Shipment
By sea, by air, by express, as customers request.
5 FAQs of Industrial Ball Mill Mineral Grindingfor Dry Wet Production Line – MineralProcessing
Industrial ball mills grind minerals in dry or wet production lines. Common questions about their use and performance are answered here.
What factors determine an industrial ball mill’s grinding capacity?
Grinding capacity depends on the mill’s size, material hardness, and grinding time. Larger mills handle more material. Harder minerals require longer grinding. Adjusting parameters like rotation speed and material feed rate optimizes output. Testing ensures the mill matches specific production needs.
How does dry grinding differ from wet grinding in mineral processing?
Dry grinding processes materials without water. It suits heat-sensitive minerals or water-scarce environments. Wet grinding uses water or liquid to form a slurry. This method reduces dust and improves mixing for finer particles. The choice depends on the mineral’s properties and the desired end product.
What maintenance practices extend a ball mill’s lifespan?
Regularly inspect liners and grinding media for wear. Lubricate bearings and gears to reduce friction. Check seals to prevent leaks. Replace damaged parts immediately. Cleaning the mill after use avoids material buildup. Consistent maintenance prevents breakdowns and ensures stable operation.
Can industrial ball mills handle abrasive materials?
Yes. Ball mills are built with wear-resistant materials like manganese steel or rubber liners. These components withstand abrasion from hard minerals. Using appropriate grinding media and timely replacements maintains efficiency. High abrasion resistance is critical for processing materials like quartz or granite.
How is energy consumption managed in industrial ball mills?
Energy use depends on mill design and operational settings. Optimize rotation speed to balance grinding efficiency and power use. Overloading the mill increases energy waste. Modern mills feature energy-saving motors and automated controls. Proper material loading and regular maintenance further reduce consumption.
(Industrial Ball Mill Mineral Grindingfor Dry Wet Production Line – MineralProcessing)
REQUEST A QUOTE
RELATED PRODUCTS
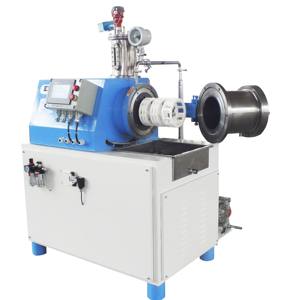
High manganese casting ball mill parts mill impact liner plate and blow bar
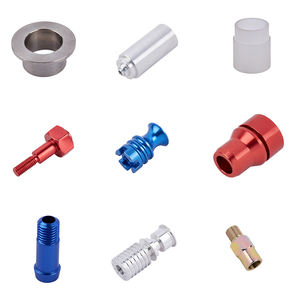
Ball Mill Working Principle, Milling Machine Tube, Overflow Ball Mill
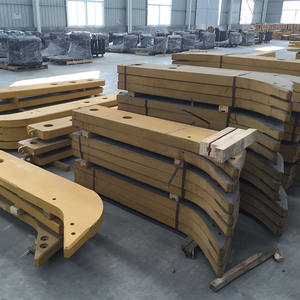
Industrial ball mill grinding machinery equipment wet and dry cement dressing crushing
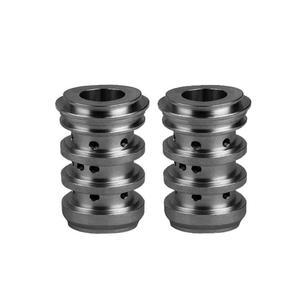
Mining Equipment Spares Hollow Shaft Discharge Shaft for Ball Mill
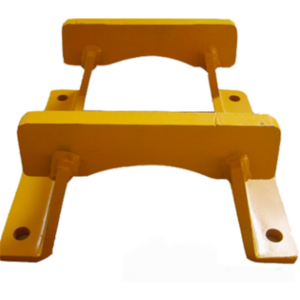
Lab Ball Mill Machine Mill Stone Gold Ore Ball Mill Liner Wear Plate Spare Parts
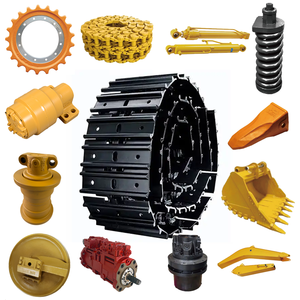