PRODUCT PARAMETERS
Description
Brief introduction of Low Whole Cement Ball Mill Grinding Ball for Ball Mill for
Ball mill is a kind of equipment used to crush or grind materials to very fine powder, which is widely used in mining, cement, chemical industry, etc. Low Whole Cement Ball Mill Grinding Ball for Ball Mill for refers to all kinds of parts and components which are necessary to ensure the normal operation of the ball mill, including liner plate, grinding balls, gears, bearings and so on.
Features and advantages of Low Whole Cement Ball Mill Grinding Ball for Ball Mill for
Strong durability: Made of high-quality materials and under strict quality control, it ensures high wear resistance and long service life of spare parts.
Good interchangeability: The standardized design makes the spare parts interchangeable between different types of ball mills, simplifying the maintenance process.
Optimized design: Customised design according to the actual working conditions, which improves the working efficiency and reduces energy consumption at the same time.
Easy to install and maintain: reasonable structure, convenient for users to quickly replace and repair, reduce downtime.
Stable performance: Precision machining and rigorous testing ensure stable performance even in harsh environments.
(Low Whole Cement Ball Mill Grinding Ball for Ball Mill for )
Specification of Low Whole Cement Ball Mill Grinding Ball for Ball Mill for
The Reduced Whole Concrete Sphere Mill Grinding Ball is made for cement manufacturing and mineral processing. It operates in round mills to grind basic materials into great powder. The product guarantees effective grinding performance and lengthy life span. The product make-up uses high-quality alloy steel. Chromium and manganese elements are included in enhance firmness and use resistance. The firmness degree reaches 58-65 HRC. This reduces contortion and fracturing throughout operation. Influence toughness is tested under hefty tons. It keeps architectural stability under duplicated collisions.
The grinding sphere comes in numerous dimensions. Sizes range from 20 mm to 120 mm. This suits different mill specs and grinding phases. Surface area smoothness is prioritized. Precision machining ensures marginal surface flaws. Satiation tolerance is controlled within 0.5%. This enhances grinding efficiency and reduces power waste.
Production involves sophisticated heat treatment procedures. Satiating and solidifying modern technologies optimize inner tension circulation. This balances solidity and sturdiness. Quality checks consist of spectroscopic evaluation and firmness testing. Each batch is inspected for uniformity. Defective products are removed prior to packaging.
The grinding round matches dry and wet grinding atmospheres. It works with cement clinker, coal, and ores. Applications cover concrete plants, power stations, and mining operations. Put on price is checked to be 10-15% lower than typical items. This extends substitute intervals and cuts maintenance prices.
Product packaging choices include woven bags or steel drums. Custom-made labeling is offered for mass orders. Storage recommendations stress dry, ventilated locations. Exposure to moisture or corrosive compounds is dissuaded.
The product meets international standards like ISO 9001 and ASTM. Environmental conformity ensures no unsafe materials are utilized. Recycling programs are supported for used grinding spheres. This reduces hazardous waste and advertises sustainability.
Efficiency data is provided for technological analyses. Customers can request samples for on-site testing. Technical assistance aids with mill optimization and product choice.
(Low Whole Cement Ball Mill Grinding Ball for Ball Mill for )
Applications of Low Whole Cement Ball Mill Grinding Ball for Ball Mill for
Reduced whole concrete sphere mill grinding spheres are crucial parts in industrial grinding systems. These rounds crush and grind resources right into fine powders. They work in ball mills for concrete production, mining, and various other sectors. Their design focuses on resilience and efficiency. Made from low alloy steel, they manage high-impact pressures and abrasive products. The heat therapy process makes certain hardness and strength. This makes them last longer than routine grinding media.
Concrete plants make use of these rounds to refine raw materials like sedimentary rock and clay. They transform these products right into raw dish for clinker manufacturing. The balls also grind clinker into concrete powder. Their consistent size and shape boost grinding efficiency. This decreases energy use and improves result. Mines rely upon them to squash ores and minerals. The balls break down acid rocks right into smaller sized bits for further handling. This step is vital for drawing out steels and minerals.
Thermal nuclear power plant make use of these grinding balls to grate coal. Great coal powder burns much more effectively in boilers. This increases power generation and cuts gas waste. Chemical plants apply them to grind resources for plant foods and ceramics. The spheres’ resistance to corrosion and put on suits extreme chemical environments.
Reduced whole concrete ball mill grinding rounds reduced maintenance expenses. Their solid construct decreases replacement regularity. This reduces downtime and labor costs. Their smooth surface area lessens friction inside the mill. Less friction indicates reduced power consumption. This lines up with sustainability objectives by lowering carbon footprints.
These spheres supply expense financial savings gradually. Their lengthy life expectancy balances the initial investment. Industries conserve cash on frequent media replacements. They additionally enhance product top quality. Regular particle size makes certain consistent final product. This is important for cement strength and chain reaction.
The rounds’ green style sustains eco-friendly production. Less worldly waste and energy make use of benefit the atmosphere. Their manufacturing procedure focuses on reducing resource usage. This makes them a responsible choice for markets aiming to meet environmental requirements.
Company Introduction
Established in 2007, Excavator Attachments Heavy Machinery Co.,ltd. focus on metal research and mining machinery spare parts. 2 factories over an area of 13,300 square meters, based on 100+ sets of equipment, our production capacity reaches 12000 Tons/Year. has passed ISO 9001 quality managment system certification in 2008.
Our mainly products are dragline excavator spare parts,rotary kiln spare parts, large modulus gear (gear shaft), gearbox ect. 40+ patents with over 45 years experience to help focus on improve the service life of spare parts. We belive that more than 80% reason of mechanical parts’ working life depends on hot processing (steel making/forging/casting/welding/heat treatment). Eight material engineers will control the quality from the original resource.
If you are interested, please feel free to contact us.
Payment
L/C, T/T, Western Union, Paypal, Credit Card etc.
Shipment
By sea, by air, by express, as customers request.
5 FAQs of Low Whole Cement Ball Mill Grinding Ball for Ball Mill for
Low chrome cement ball mill grinding balls are wear-resistant materials made from low chromium alloy steel. They are used in ball mills for grinding cement clinker and raw materials. These balls have good hardness and toughness. They resist wear well under harsh grinding conditions. Their lower chromium content makes them cost-effective compared to high chrome alternatives.
What benefits do low chrome grinding balls offer? They balance performance and cost. Their hardness ensures efficient grinding of cement materials. They last long in abrasive environments. They cost less than high chrome balls but still handle typical cement milling demands. This makes them a practical choice for many cement plants.
How long do low chrome balls last in a ball mill? Their lifespan varies based on material quality and operating conditions. On average, they last between 2,000 to 5,000 hours. Factors like mill speed, feed size, and maintenance practices affect durability. Regular checks help maximize their service life.
Can low chrome balls work in different types of ball mills? Yes. They suit most cement ball mills, including horizontal and vertical designs. Compatibility depends on mill specifications and grinding requirements. Always confirm with the manufacturer if unsure. Proper sizing ensures optimal grinding efficiency.
What maintenance is needed for low chrome grinding balls? Inspect them regularly for wear or cracks. Replace damaged balls promptly to avoid mill inefficiency. Keep the mill clean to reduce contamination. Monitor grinding patterns to adjust the ball charge as needed. Proper maintenance keeps the milling process stable and productive.
(Low Whole Cement Ball Mill Grinding Ball for Ball Mill for )
REQUEST A QUOTE
RELATED PRODUCTS
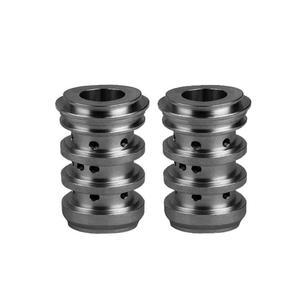
s Large diameter ball mill bull gear forging ZG45 cement rotary kiln spur girth ring
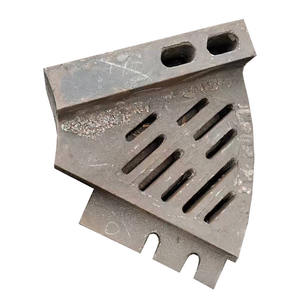
Low worth buying products Mining Grinding Mill Trommel Scrubber Wear Parts Rubber Ball Mill Liner For
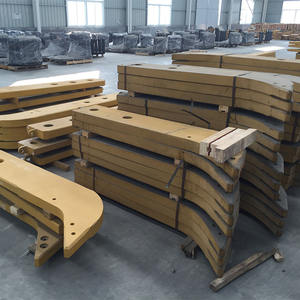
Factory low 1-5tph ball mill grinding machine for grinding stone rock gold ore
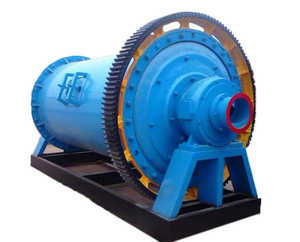
Rotary kiln and cement ball mill spare pasts large steel spur gear wheel and ring gear casting girth gear
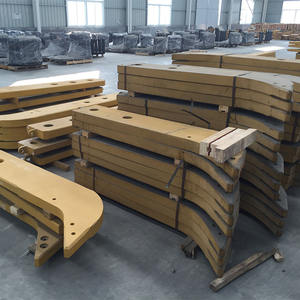
Good quality grinding mill Ball Mill Classifier System
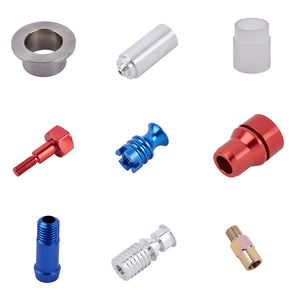