PRODUCT PARAMETERS
Description
Brief introduction of Ore Ball Mill Silica Ball Mill Powder Making Ball Mill
Ball mill is a kind of equipment used to crush or grind materials to very fine powder, which is widely used in mining, cement, chemical industry, etc. Ore Ball Mill Silica Ball Mill Powder Making Ball Mill refers to all kinds of parts and components which are necessary to ensure the normal operation of the ball mill, including liner plate, grinding balls, gears, bearings and so on.
Features and advantages of Ore Ball Mill Silica Ball Mill Powder Making Ball Mill
Strong durability: Made of high-quality materials and under strict quality control, it ensures high wear resistance and long service life of spare parts.
Good interchangeability: The standardized design makes the spare parts interchangeable between different types of ball mills, simplifying the maintenance process.
Optimized design: Customised design according to the actual working conditions, which improves the working efficiency and reduces energy consumption at the same time.
Easy to install and maintain: reasonable structure, convenient for users to quickly replace and repair, reduce downtime.
Stable performance: Precision machining and rigorous testing ensure stable performance even in harsh environments.
(Ore Ball Mill Silica Ball Mill Powder Making Ball Mill)
Specification of Ore Ball Mill Silica Ball Mill Powder Making Ball Mill
The Ore Sphere Mill, Silica Sphere Mill, and Powder Making Ball Mill are industrial grinding equipments made for processing different products right into great powders. These mills are commonly utilized in mining, construction, porcelains, and chemical markets as a result of their performance, longevity, and adaptability. Below are the essential specifications and attributes of these round mills.
The Ore Round Mill is crafted to grind ores such as gold, copper, iron, and various other metallic or non-metallic minerals. It normally runs with a drum rotation rate of 15-35 rpm, powered by an electric motor ranging from 18.5 kW to 4500 kW, relying on the model dimension. The mill’s capacity differs from 0.65 t/h to 350 t/h, accommodating both small laboratories and large industrial operations. It makes use of steel balls of differing sizes (25-150 mm) as grinding media, making certain efficient pulverization. The drum is created from top notch steel with wear-resistant linings, enhancing longevity. Ore sphere mills sustain both completely dry and damp grinding, with discharge options consisting of grate kind and overflow type to fit various material fineness requirements.
The Silica Ball Mill is specialized for grinding silica sand, quartz, and comparable products right into ultra-fine powders used in glass, porcelains, and construction. It features a somewhat higher turning rate (20-38 rpm) to accomplish finer fragment dimensions, usually below 45 microns. The electric motor power ranges from 22 kW to 4000 kW, with abilities covering 1 t/h to 300 t/h. The lining and grinding media are usually constructed from alumina or silica-based products to minimize contamination. Temperature control systems are incorporated to stop overheating, protecting silica’s chemical residential properties.
The Powder Making Round Mill is a versatile design for generating powders of materials like concrete, sedimentary rock, clay, and chemicals. It supports flexible excellence from 50 mesh to 300 mesh, with motor power between 15 kW and 2100 kW. The drum diameter and size ratios are optimized for exact grinding, and it uses advanced sealing systems to lower dust leak. This mill supports both continual and set procedures, catering to diverse manufacturing needs.
Common attributes across these sphere mills consist of robust building and construction, low upkeep demands, energy-efficient styles, and compatibility with supporting tools like classifiers or dirt collectors. They are customizable in size, drive systems (equipment drive or pulley drive), and automation abilities for contemporary industrial configurations. Safety and security features such as emergency stops and overload defense make certain trusted procedure. These mills are suitable for markets focusing on constant bit size circulation, high throughput, and long-lasting functional reliability.
(Ore Ball Mill Silica Ball Mill Powder Making Ball Mill)
Applications of Ore Ball Mill Silica Ball Mill Powder Making Ball Mill
Applications of Ore Round Mill, Silica Round Mill, and Powder Making Ball Mill span different markets, providing reliable solutions for material grinding and refining. Ore Sphere Mills are mostly made use of in mining and metallurgy to grind ores such as gold, copper, iron, and zinc right into fine fragments. This process frees useful minerals from raw ore, allowing efficient extraction during flotation, seeping, or smelting. These mills are crucial in mineral handling plants, handling unpleasant products with durable construction and continuous operation. They ensure uniform bit size distribution, boosting downstream recuperation rates. Industries like cement manufacturing additionally utilize Ore Round Mills for clinker grinding, adding to durable building and construction materials. Silica Ball Mills focus on handling silica sand into ultra-fine powders, crucial for high-purity applications. They are indispensable to glass production, where carefully ground silica ensures quality and strength in glass products. Ceramics manufacturing depends on these mills to attain the precise bit dimension needed for lusters and ceramic bodies, improving item quality and thermal stability. In building, silica powder from these mills enhances concrete and refractory materials. The mills’ ability to preserve contamination-free grinding is vital for electronics-grade silica used in semiconductors. Powder Making Ball Mills are flexible equipments developed for producing great powders throughout sectors. They process products like quartz, feldspar, limestone, and pigments, dealing with industries such as paints, finishings, and drugs. In cosmetics, these mills grind talc and mica to achieve smooth structures in make-up products. Chemical industries use them to grate basic materials for catalysts or plant foods. Flexible speed and grinding media enable modification of fineness, conference particular production needs. All three round mill types highlight energy efficiency, toughness, and reduced upkeep. Their closed-circuit systems decrease dirt, sustaining environmentally friendly procedures. By allowing accurate control over fragment size and uniformity, these mills improve item efficiency and process effectiveness, making them important in industrial production and material handling.
Company Introduction
Established in 2007, Excavator Attachments Heavy Machinery Co.,ltd. focus on metal research and mining machinery spare parts. 2 factories over an area of 13,300 square meters, based on 100+ sets of equipment, our production capacity reaches 12000 Tons/Year. has passed ISO 9001 quality managment system certification in 2008.
Our mainly products are dragline excavator spare parts,rotary kiln spare parts, large modulus gear (gear shaft), gearbox ect. 40+ patents with over 45 years experience to help focus on improve the service life of spare parts. We belive that more than 80% reason of mechanical parts’ working life depends on hot processing (steel making/forging/casting/welding/heat treatment). Eight material engineers will control the quality from the original resource.
If you are interested, please feel free to contact us.
Payment
L/C, T/T, Western Union, Paypal, Credit Card etc.
Shipment
By sea, by air, by express, as customers request.
5 FAQs of Ore Ball Mill Silica Ball Mill Powder Making Ball Mill
What is the primary function of an Ore Ball Mill, Silica Ball Mill, and Powder Making Ball Mill?
The Ore Ball Mill is designed to grind ores and raw materials into fine powder for mineral processing, metallurgy, and chemical industries. The Silica Ball Mill specializes in grinding silica-rich materials like quartz and sand, commonly used in glass, ceramics, and construction. The Powder Making Ball Mill focuses on producing ultra-fine powders for coatings, cosmetics, pharmaceuticals, and advanced materials, ensuring consistent particle size distribution.
How does a ball mill work to grind materials into powder?
Ball mills operate by rotating a cylindrical chamber filled with grinding media, such as steel or ceramic balls. As the cylinder rotates, the balls cascade and impact the material, crushing it into finer particles. The grinding process combines abrasion, impact, and attrition forces to reduce material size. For silica and ore mills, dry or wet grinding methods are used, while powder-making mills often optimize speed and media size for ultra-fine output.
What materials can be processed using these ball mills?
Ore Ball Mills handle metals like gold, copper, and iron ore, along with non-metallic minerals. Silica Ball Mills process silica sand, quartz, and feldspar for glass or ceramic production. Powder Making Ball Mills work with softer materials such as limestone, gypsum, talc, and pigments. All mills require materials to be within specific hardness and moisture ranges to ensure efficient grinding and avoid equipment damage.
What are the key maintenance requirements for these ball mills?
Regular lubrication of gears and bearings is critical. Inspect and replace worn liners, grinding media, and seals to prevent leaks. Clean the mill interior to avoid material buildup, and check alignment and belt tension. For silica mills, ensure dust-control systems function to minimize inhalation risks. Schedule routine downtime for vibration checks and motor inspections to maintain operational safety and efficiency.
What advantages do these ball mills offer over other grinding methods?
Ball mills provide high grinding efficiency with low energy consumption, especially for large-scale operations. They produce uniform particle sizes and handle both dry and wet materials. Their versatility allows customization of media type, rotation speed, and liner materials to suit different applications. Durability and simple design reduce long-term costs, while closed-circuit systems enable continuous processing with minimal manual intervention.
(Ore Ball Mill Silica Ball Mill Powder Making Ball Mill)
REQUEST A QUOTE
RELATED PRODUCTS

Ball mill wear-resistant parts high chromium solid steel ball steel section cast alloy steel ball
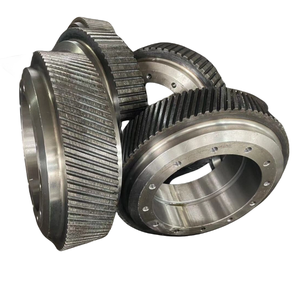
Low Used 500kg Ball Mill Spare Parts Drawing
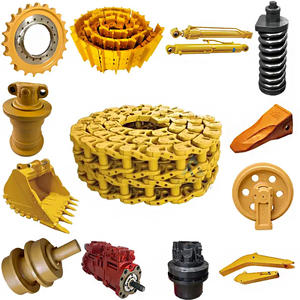
Ball mill Spare parts ball mill liner accessories ball mill liner plate
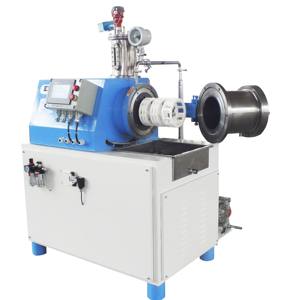
High manganese casting ball mill parts mill impact liner plate and blow bar
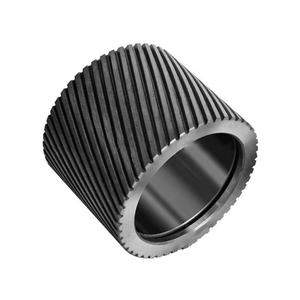
Superir Hot Low Ball Mill Grinding Machine With Lower Starting Power
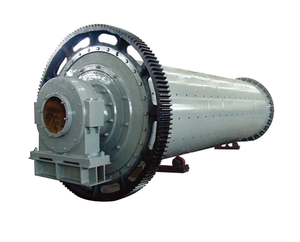