PRODUCT PARAMETERS
Description
Brief introduction of Rotary Kiln And Cement Ball Mill Spare Pasts Ring Gear Casting Girth Gear
Ball mill is a kind of equipment used to crush or grind materials to very fine powder, which is widely used in mining, cement, chemical industry, etc. Rotary Kiln And Cement Ball Mill Spare Pasts Ring Gear Casting Girth Gear refers to all kinds of parts and components which are necessary to ensure the normal operation of the ball mill, including liner plate, grinding balls, gears, bearings and so on.
Features and advantages of Rotary Kiln And Cement Ball Mill Spare Pasts Ring Gear Casting Girth Gear
Strong durability: Made of high-quality materials and under strict quality control, it ensures high wear resistance and long service life of spare parts.
Good interchangeability: The standardized design makes the spare parts interchangeable between different types of ball mills, simplifying the maintenance process.
Optimized design: Customised design according to the actual working conditions, which improves the working efficiency and reduces energy consumption at the same time.
Easy to install and maintain: reasonable structure, convenient for users to quickly replace and repair, reduce downtime.
Stable performance: Precision machining and rigorous testing ensure stable performance even in harsh environments.
(Rotary Kiln And Cement Ball Mill Spare Pasts Ring Gear Casting Girth Gear)
Specification of Rotary Kiln And Cement Ball Mill Spare Pasts Ring Gear Casting Girth Gear
The Rotary Kiln and Cement Ball Mill Spare Parts, specifically the Ring Gear Casting Girth Gear, are critical components in the cement manufacturing process, designed to ensure the smooth and efficient operation of rotary kilns and ball mills. These gears are engineered to withstand extreme conditions, including high temperatures, heavy loads, and continuous rotational stress, making them indispensable in the cement production industry.
The Ring Gear, also known as the Girth Gear, is a large, precision-cast component that meshes with the pinion gear to transmit rotational motion to the rotary kiln or ball mill. It is typically manufactured from high-quality alloy steel or cast iron, ensuring exceptional durability and resistance to wear and tear. The gear teeth are meticulously machined to exact specifications, ensuring optimal meshing with the pinion gear and minimizing friction, which enhances the overall efficiency of the system.
One of the key features of the Girth Gear is its robust construction, which allows it to handle the immense torque generated during the operation of rotary kilns and ball mills. The gear is often heat-treated to improve its hardness and toughness, further extending its service life. Additionally, the gear is designed with precise tolerances to ensure smooth operation and reduce the risk of misalignment, which can lead to premature wear or failure.
The Girth Gear is available in various sizes and configurations to suit different types of rotary kilns and ball mills, making it a versatile solution for a wide range of applications. It is also designed for easy installation and maintenance, reducing downtime and ensuring continuous operation.
In summary, the Ring Gear Casting Girth Gear is a vital component in the cement manufacturing process, offering unmatched durability, precision, and performance. Its high-quality construction and precise engineering make it an essential spare part for maintaining the efficiency and reliability of rotary kilns and ball mills in the cement industry.
(Rotary Kiln And Cement Ball Mill Spare Pasts Ring Gear Casting Girth Gear)
Applications of Rotary Kiln And Cement Ball Mill Spare Pasts Ring Gear Casting Girth Gear
Rotary kilns and cement ball mills are essential components in the cement manufacturing process, playing a critical role in the production of clinker and grinding of raw materials. To ensure their efficient and uninterrupted operation, high-quality spare parts like ring gears and girth gears are indispensable. These components are vital for the smooth functioning of rotary kilns and ball mills, as they facilitate the transmission of torque and rotational motion, enabling the equipment to perform at optimal levels.
Ring gears and girth gears are large, precision-engineered castings typically made from high-strength alloy steel or ductile iron. They are designed to withstand extreme operational conditions, including high temperatures, heavy loads, and continuous rotational stress. The durability and reliability of these gears are crucial for minimizing downtime and maintenance costs in cement plants. Their robust construction ensures long service life, even in harsh industrial environments.
One of the primary applications of ring gears and girth gears is in rotary kilns, where they are mounted on the kiln shell to drive its rotation. This rotation is essential for the calcination process, where raw materials are heated to produce clinker. Similarly, in cement ball mills, girth gears are used to drive the mill’s rotation, enabling the grinding of clinker and other materials into fine cement powder. The precise alignment and smooth operation of these gears are critical for maintaining the efficiency and productivity of the entire cement production process.
In addition to their use in cement manufacturing, ring gears and girth gears are also employed in other industries, such as mining, metallurgy, and chemical processing, where rotary equipment is utilized. Their versatility and reliability make them a key component in various heavy-duty applications.
Overall, the quality and performance of ring gears and girth gears significantly impact the operational efficiency of rotary kilns and cement ball mills. Investing in high-quality, precision-cast spare parts ensures smoother operations, reduced maintenance, and enhanced productivity in cement plants and beyond.
Company Introduction
Established in 2007, Excavator Attachments Heavy Machinery Co.,ltd. focus on metal research and mining machinery spare parts. 2 factories over an area of 13,300 square meters, based on 100+ sets of equipment, our production capacity reaches 12000 Tons/Year. has passed ISO 9001 quality managment system certification in 2008.
Our mainly products are dragline excavator spare parts,rotary kiln spare parts, large modulus gear (gear shaft), gearbox ect. 40+ patents with over 45 years experience to help focus on improve the service life of spare parts. We belive that more than 80% reason of mechanical parts’ working life depends on hot processing (steel making/forging/casting/welding/heat treatment). Eight material engineers will control the quality from the original resource.
If you are interested, please feel free to contact us.
Payment
L/C, T/T, Western Union, Paypal, Credit Card etc.
Shipment
By sea, by air, by express, as customers request.
5 FAQs of Rotary Kiln And Cement Ball Mill Spare Pasts Ring Gear Casting Girth Gear
Rotary kilns and cement ball mills are essential components in the cement manufacturing process, and their efficient operation relies heavily on high-quality spare parts like ring gears and girth gears. Here are five frequently asked questions about these critical components:
1. **What is a girth gear, and why is it important in rotary kilns and ball mills?**
A girth gear, also known as a ring gear, is a large, circular gear that is mounted around the circumference of a rotary kiln or ball mill. It plays a crucial role in transmitting torque from the drive system to the rotating drum, ensuring smooth and consistent operation. Without a properly functioning girth gear, the entire system can experience downtime, leading to significant production losses.
2. **What materials are used to manufacture girth gears?**
Girth gears are typically made from high-quality alloy steel or cast iron, which are chosen for their durability, strength, and resistance to wear and tear. The materials are carefully selected to withstand the heavy loads, high temperatures, and harsh operating conditions commonly found in cement plants.
3. **How often do girth gears need maintenance or replacement?**
The lifespan of a girth gear depends on factors such as operating conditions, load, and maintenance practices. Regular inspections and proper lubrication can extend the gear’s life. However, due to the high stress and wear they endure, girth gears may need replacement every 5 to 10 years, depending on usage.
4. **What are the common issues with girth gears, and how can they be prevented?**
Common issues include wear, misalignment, and tooth damage. These problems can be minimized through proper installation, regular alignment checks, and consistent lubrication. Using high-quality gears and adhering to maintenance schedules can also prevent premature failure.
5. **Can girth gears be customized for specific applications?**
Yes, girth gears can be customized to meet the specific requirements of different rotary kilns and ball mills. Factors such as size, material, tooth profile, and hardness can be tailored to ensure optimal performance and compatibility with the equipment.
In summary, girth gears are vital components in rotary kilns and cement ball mills, and their proper selection, maintenance, and replacement are key to ensuring efficient and uninterrupted cement production. Investing in high-quality gears and adhering to best practices can significantly enhance the longevity and performance of these critical systems.
(Rotary Kiln And Cement Ball Mill Spare Pasts Ring Gear Casting Girth Gear)
REQUEST A QUOTE
RELATED PRODUCTS
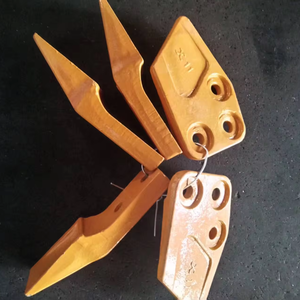
Ball Mill 6 Ball Mill Parts Gear Aluminum Powder Ball Mill 1200*4500
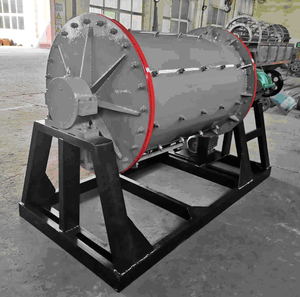
Ceramic Liner Ball Mill Machine Ball Grinding Mill Small Laboratory Ball Mill From
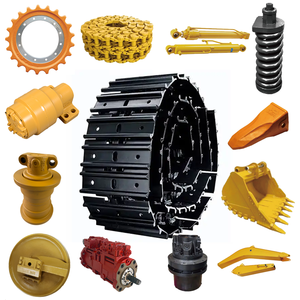
Mineral Ball Mill Spare Parts Gold Grinder Ball Mills Machine Metal Ball Mill for Gold Mining
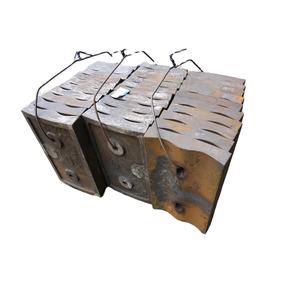
Horizontal PTFE Grinding Jars Ball Mill Parts Used For Laboratory Roller Milling Machine Alumina Grinding Jar Mill
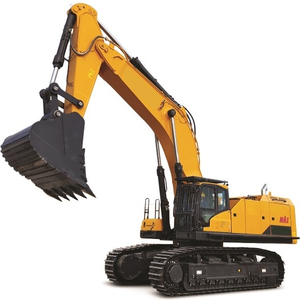
super good quality industrial Resistant Mining Spare Parts ball mill rubber lining
