PRODUCT PARAMETERS
Description
Introduction to towed Excavator Parts Undercarriage Components Sprocket Segment D6H D6R Segment
A towed excavator, also known as a tracked or tire mobile excavator, is a type of heavy equipment that is widely used in the construction and mining sectors.Excavator Parts Undercarriage Components Sprocket Segment D6H D6R Segment refers to a variety of parts that are used to maintain, repair, or replace worn-out parts of this machine.
Features and advantages of towed Excavator Parts Undercarriage Components Sprocket Segment D6H D6R Segment
Durability: made of high-quality materials to ensure long life and high durability.
Compatibility: Designed to meet OEM specifications for a wide range of makes and models.
Economical: Third-party spare parts are usually less expensive compared to OEM parts.
Ease of Replacement: Standardised design allows for quick and easy installation and replacement.
Reliability: rigorously tested to ensure stable and reliable performance.
(Excavator Parts Undercarriage Components Sprocket Segment D6H D6R Segment)
Specification of Excavator Parts Undercarriage Components Sprocket Segment D6H D6R Segment
The sprocket segment is a critical component in the undercarriage system of Caterpillar D6H and D6R excavators, designed to ensure efficient power transmission and longevity in demanding operating conditions. These segments engage with the track chain links, driving the excavator’s movement while maintaining alignment and reducing wear on adjacent undercarriage parts. Compatible with D6H and D6R models, these sprocket segments are precision-engineered to match OEM specifications, guaranteeing seamless integration and optimal performance. Constructed from high-grade alloy steel, the segments undergo heat treatment and surface hardening processes to achieve a hardness range of 45-50 HRC, enhancing resistance to abrasion, impact, and fatigue. This ensures durability in rugged environments such as mining, construction, and earthmoving applications. The sprocket teeth are machined to precise tolerances, minimizing track slippage and uneven wear while maximizing power transfer efficiency. Each segment features a segmented design, allowing for individual replacement without disassembling the entire sprocket assembly, which reduces downtime and maintenance costs. The bolt holes are pre-drilled and aligned to ensure secure fastening and proper alignment with the sprocket hub. Key specifications include a tooth count optimized for D6H/D6R track chains (typically 9-12 teeth per segment, depending on configuration), a pitch diameter matching the track chain’s pitch, and a weight of approximately 15-20 kg per segment for ease of handling. The inner and outer diameters are tailored to fit the sprocket hub dimensions, while the bolt circle diameter (BCD) ensures compatibility with existing hardware. These segments are built to withstand heavy loads, mud, rocks, and debris, making them ideal for extreme-duty applications. Regular inspection and timely replacement of worn sprocket segments are recommended to prevent accelerated wear on track chains, rollers, and idlers. By using genuine or high-quality aftermarket sprocket segments, operators can extend the undercarriage’s service life, improve machine stability, and reduce long-term operational costs.
(Excavator Parts Undercarriage Components Sprocket Segment D6H D6R Segment)
Applications of Excavator Parts Undercarriage Components Sprocket Segment D6H D6R Segment
The Applications of Excavator Undercarriage Components: Sprocket Segments for D6H and D6R Models
Excavator undercarriage components play a critical role in ensuring the stability, mobility, and longevity of heavy machinery. Among these components, sprocket segments—specifically designed for Caterpillar D6H and D6R excavators—are vital for transferring power from the drive system to the track chains, enabling smooth movement across rugged terrains. These segments are engineered to endure extreme conditions, making them indispensable in industries like construction, mining, forestry, and road building.
In mining operations, D6H and D6R sprocket segments face abrasive materials, heavy loads, and prolonged use. Their high-strength, heat-treated steel construction resists wear, reducing the risk of premature failure. Similarly, in construction projects, uneven surfaces and debris-laden environments demand components that maintain alignment and minimize stress on adjacent parts. Precision-machined sprocket segments ensure seamless engagement with track links, preventing slippage and enhancing operational efficiency.
The segmented design of these components offers practical advantages. Instead of replacing an entire sprocket, operators can swap out individual worn segments, cutting downtime and repair costs. This modularity is particularly beneficial in remote or time-sensitive projects, such as disaster recovery or large-scale earthmoving, where equipment availability is crucial.
Durability is further enhanced through advanced manufacturing techniques. Case-hardened surfaces and corrosion-resistant treatments extend service life, even in wet or chemically aggressive environments like quarries or demolition sites. Consistent performance of these sprocket segments also reduces strain on other undercarriage parts, such as rollers and idlers, lowering overall maintenance expenses.
For D6H and D6R excavators, using genuine or premium aftermarket sprocket segments ensures compatibility and optimal power transmission. Worn segments can lead to track misalignment, increased fuel consumption, and accelerated component wear. Timely replacement maintains traction, minimizes operational disruptions, and safeguards against costly breakdowns.
In summary, D6H and D6R sprocket segments are engineered for reliability in high-stress applications. Their robust design, ease of maintenance, and role in preserving excavator performance make them a critical investment for industries reliant on heavy machinery. By prioritizing quality in these components, operators maximize productivity and reduce long-term operational costs.
Company Introduction
Established in 2007, Excavator Attachments Heavy Machinery Co.,ltd. focus on metal research and mining machinery spare parts. 2 factories over an area of 13,300 square meters, based on 100+ sets of equipment, our production capacity reaches 12000 Tons/Year. has passed ISO 9001 quality managment system certification in 2008.
Our mainly products are dragline excavator spare parts,rotary kiln spare parts, large modulus gear (gear shaft), gearbox ect. 40+ patents with over 45 years experience to help focus on improve the service life of spare parts. We belive that more than 80% reason of mechanical parts’ working life depends on hot processing (steel making/forging/casting/welding/heat treatment). Eight material engineers will control the quality from the original resource.
If you are interested, please feel free to contact us.
Payment
L/C, T/T, Western Union, Paypal, Credit Card etc.
Shipment
By sea, by air, by express, as customers request.
5 FAQs of Excavator Parts Undercarriage Components Sprocket Segment D6H D6R Segment
**What is the purpose of a sprocket segment in an excavator undercarriage?**
The sprocket segment is a critical component that engages with the track links to drive the excavator’s movement. It transfers power from the final drive to the tracks, ensuring smooth operation over rough terrain. For the D6H and D6R models, the sprocket segment must align precisely with the track chain to minimize wear and maintain efficiency.
**Are D6H and D6R sprocket segments interchangeable?**
While both models share similarities, sprocket segments for the D6H and D6R are designed to match specific track chain configurations. Compatibility depends on the exact part number and machine specifications. Always verify the segment’s compatibility with your excavator’s model and serial number before purchasing to avoid installation issues or premature wear.
**What materials are used in high-quality sprocket segments?**
Premium sprocket segments for D6H/D6R excavators are forged from high-carbon or alloy steel, heat-treated for hardness and durability. This ensures resistance to abrasion, impact, and extreme loads. Look for segments with precision machining to guarantee proper fitment and reduced stress on adjacent undercarriage components.
**How often should sprocket segments be inspected or replaced?**
Inspect sprocket segments during routine undercarriage maintenance, typically every 250–500 operating hours. Replace them if teeth show excessive wear (over 30% loss), cracks, or deformation. Delaying replacement can damage the track chain, idlers, and final drive, leading to costly repairs. Operating conditions (e.g., abrasive terrain) may shorten lifespan.
**Can I replace a single sprocket segment, or must the entire set be changed?**
While replacing a single damaged segment is possible, it’s recommended to replace all segments as a set to ensure uniform wear and balanced performance. Mixing old and new segments may cause uneven tension, accelerating wear on tracks and other components. For D6H/D6R models, follow OEM guidelines for optimal undercarriage longevity.
**Where can I source genuine or reliable aftermarket sprocket segments?**
Reputable suppliers offer OEM-compliant segments for D6H/D6R excavators, tested for material integrity and dimensional accuracy. Ensure the supplier provides certifications, warranties, and technical support. Aftermarket options can be cost-effective but verify they meet or exceed original specifications for performance and safety.
(Excavator Parts Undercarriage Components Sprocket Segment D6H D6R Segment)
REQUEST A QUOTE
RELATED PRODUCTS
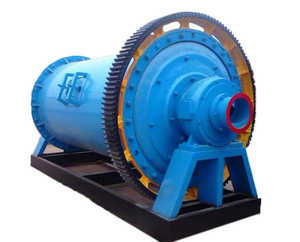
Professional Factory Reliable Performance Stable Structure Diesel Engine Parts For Excavators
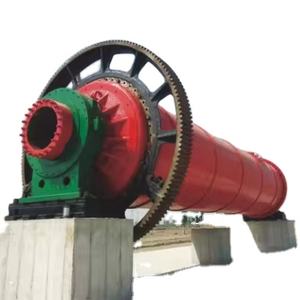
Construction Machinery Parts QSL8.9 Diesel Engine Excavator Assembly for Cummins
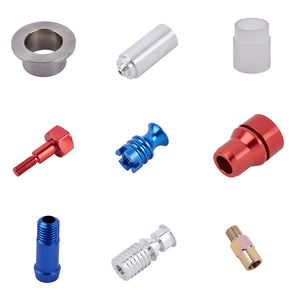
Excavator Part Komatsu PC360-7 Fuel Line Clamp 07285-00080
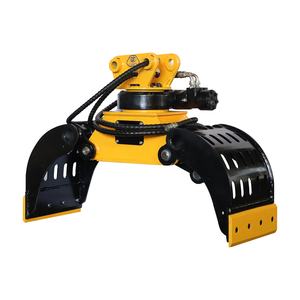
CE/ISO9001 Attachment For excavator
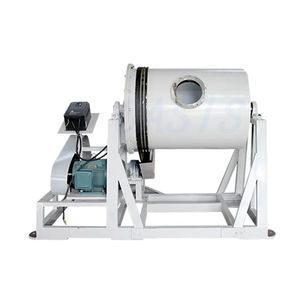
High Quality Excavator Spare Parts And Replaceable Design Heavy Duty Bucket Tooth
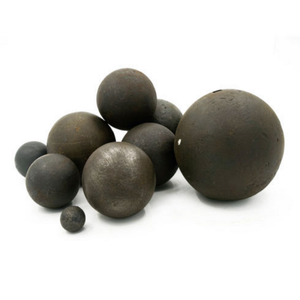